MIM 316
MIM 316 Introduction
MIM 316L is an austenitic grade and food grade stainless steel, it is suitable for applications with extremely high corrosion resistance. This grade stainless steel also has properties of excellent elongation and ductility, non-magnetic. MIM 316L is applied widely in the food, marine and medical industry.
Stainless steel 316L has characteristic high strength and corrosion resistance. Therefore, it is widely used for components in food and potable water storage. These properties are critical for metal with acids contacting. The high alloy and low carbon content of stainless steel 316L is great fit for food grade applications.
Stainless steel 316L has high corrosion resistance, ductility and good polishing characteristics, while has lower strength and hardness than heat treatable stainless steel like 17-4 PH, 420 and 440C. MIM 316L is suitable for applications with attractive surface finish requirements, such as consumer products of wristwatches. Furthermore, it is also suitable for applications with superior corrosion properties, such as medical devices and dental components. The high sintered density with stainless steel 316L minimize surface porosity, in order to inhibit contaminants accumulation and achieve high hygiene standard.
Chemical Composition
The common composition of MIM 316L after sitering is as following:
Stainless steel 316L | Iron | Nickel | Molybdenum | Silicon | Carbon | Chromium | Phosphorus | Manganese | Nitrogen | Sulfur |
Percent by Weight | BaL. | 10.00-14.00 | 2.00-3.00 | 0.75 | 0.03 | 16.00-18.00 | 0.045 | 2.00 | 0.10 | 0.030 |
Typical Mechanical Properties
The typical mechanical properties of MIM 316L are as following:
Material | Density | Tensile Strength | Yield Strength(0.2%) | Impact Strength | Hardness | Elongation(% in 25.4mm) |
Stainless steel 316L | ≥7.85g/cm³ | ≥450 Mpa | ≥140Mpa | 190J | 100-150 HV10 | ≥40% |
These common properties can be adjusted to different application needs. However, it is critical to notice that all properties are inter-correlated, certain properties will offset value of other properties. For example: high hardness will influence elongation to a lower value.
As the challenge of different property requirements, we require years of design and production experience to ensure the best solution. Our professional engineering team can assist you from the early material selection and design possibility.
MIM 316 Feedstock
ZCMIM applies MIM 316L feedstock with base of nitric acid catalytic debinding system. Our professional MIM experience can realize the integrated manufacturing of precision structure. We have production advantage of wide material adaptability, high automation degree, and high batch production.
MIM 316L is used in mobile phone parts, wearable smart terminals, automotive parts, medical equipment, aerospace parts. All these parts require high strength and high toughness.
ZCMIM is able to apply different MIM 316L feedstock with specific application requirements, the types of stainless steel 316L are as following:
316L Alloy Types
Master alloy and Pre-alloy
Stainless steel in metal injection molding can apply two different alloy powders: master alloy and pre-alloy. The pre-alloy technique applies atomized powders with the exact chemical composition as the final 316L. Alternatively, the master alloy technique utilize enriched alloy powder to mix with carbonyl iron powder to achieve 316L composition after final sintering. Master alloy technology provides significant cost benefits in requirement of fine particle size (16 μm).
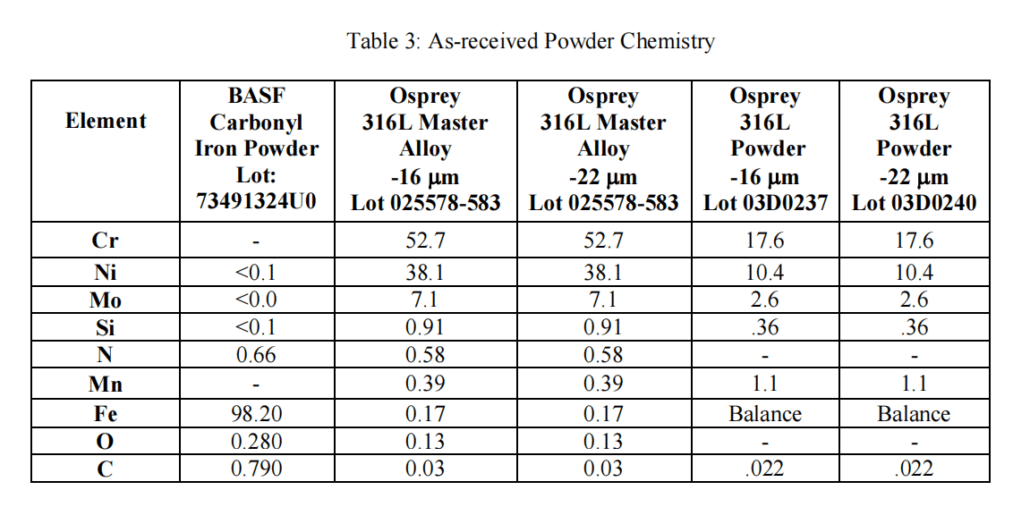
Pre-alloyed MIM 316L powders have defined specification, like chemical composition, particle size distribution, tap density. However, the chemical composition of stainless steel 316L often deviate from the international standards, especially for carbon levels.
Therefore, customized chemistry with little element variation is required to achieved final composition after sintering. Furthermore, the relatively broad Ni range from 10% to 14% result in different application properties: low nickel levels will achieve high sintered density by liquid phase sintering, high nickel level will reduce magnetic susceptibility of final sintered parts.
Different Alloy Feedstock Characteristics
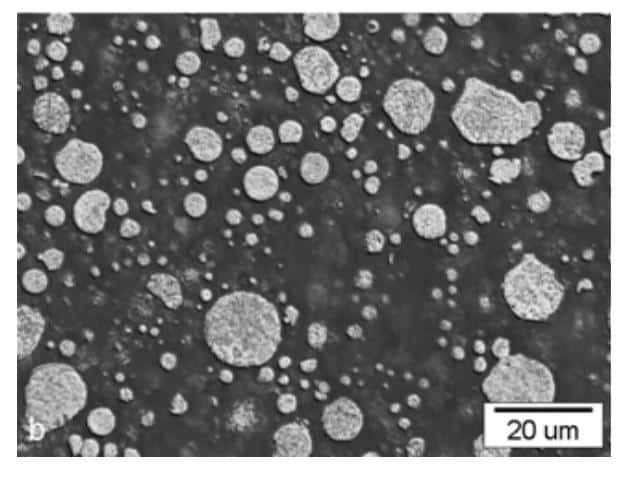
The MIM 316L feedstock has binder of approximately mass fraction 6% and volume fraction 40%. Its mixture density is almost 5.3g/cm3, the particle powder size of stainless steel powder is in different size, from 5 μm to 50 μm. The common viscosity is about 300 Pa-s at 170℃.
The following table summarize the common injection molding parameters of MIM 316L:
Parameter | 1 | 2 |
Injection molding pressure | 95 MPa | 110 MPa |
Injection speed – Vb | 20mm/s | 40mm/s |
Die/Mold temperature -To | 20 | 40 |
Melt temperature -Tt | 180 | 200 |
Holding pressure -Pn | 10MPa | 50MPa |
Time of holding pressure -tn | 3s | 7s |
Cooling time- to | 15s | 30s |
Particle Size
The particle size of alloy powders will affect the apparent viscosity. Finer powders have higher apparent viscosity, because its higher surface has less binder available for lubrication.
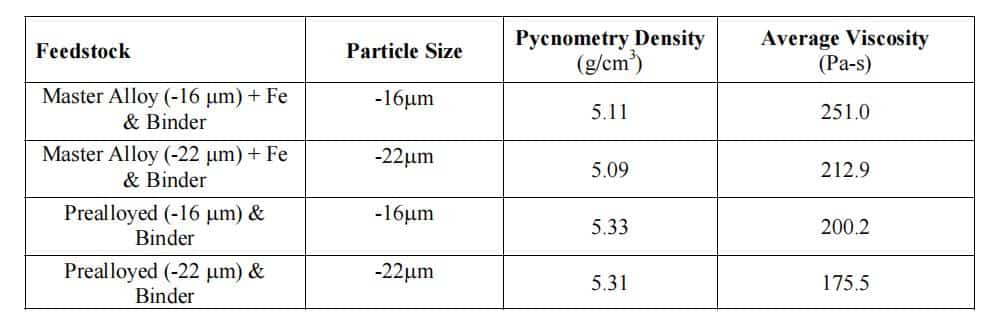
Normally, both pre-alloyed and mater alloy feedstocks have excellent molding capability. However, prealloyed feedstocks have higher tendency for powder/binder separation near gate area, while mater alloy feedstocks don’t show this effect. Comparing to pre-alloy feedstocks, mater alloy feedstocks exhibit higher transverse rupture strength on the green parts.
After typical sinter temperature of 1350℃ for MIM 316L, feedstock of different powder types can achieve 97% of wrought density. The carbon level of sintered components are both within the standard of ASTM Stainless Steel 316L, maximum carbon specification of 0.03%.
316L Sintering Parameter
The main properties of stainless steel 316L are influenced by process parameter of sintering. The mechanical properties primarily depend on the sintering density and microstructure. However, residual carbon from incomplete debinding will hinder the sintering, high-temperature vacuum sintering will cause the evaporation of volatile elements, control hard and brittle sigma phase by cooling rate,
There is a characteristic of high temperature sintering, the final sintered properties depend on not only controllable factors, but also on factors difficult to control. For MIM 316L, the main factors are injection molding parameters – pressure, temperature, sintering condition – debinding, sintering atmosphere and temperature.
Ceramic Al2O3/SiC plates are applied as support for the debinded and sintered components, in order to prevent distortion. Comparing to metallic supports, these ceramic plates are much more stable during high-temperature sintering (1350℃). The vacuum sintering is at an absolute pressure of approximately 1Pa. The sintering process for stainless steel is either super-solidus liquid-phase sintering (SLPS) or liquid-phase sintering (LPS). From thermo-dynamic calculations, most sintering is in the solid-state, as the liquid starts to form only above 1390℃.
Typical Sintering Properties
The stainless steel chemistry specification (UNS SD31603) is vary broad, its extreme properties may vary in a significant range. 316L is nominally classified as a fully austenitic alloy. But this depends on the absolute levels of Cr, Ni, Mo, and Cr/Ni ratio, delta ferritic phase are still exist in the final micro-structure.
In medical applications, especially in the vicinity of high-powered magnets (like: MRI scanners), it is essential that metal components must be non-magnetic with no residual delta ferrite. Ni content with 10-14% will promote the formation of austenite and ensure the fully austenitic microstructure after sintering.
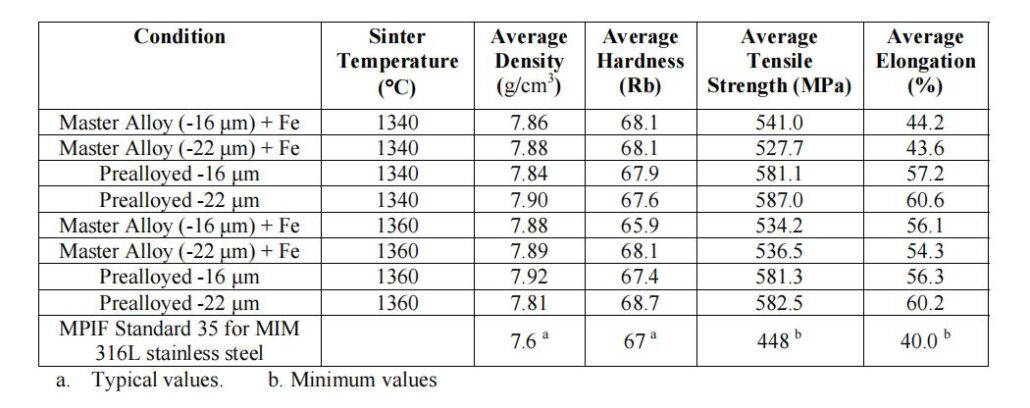
Density
The theoretical density of SS 316L is 8.0g/cm3, while the average sintered density can achieve 7.81g/cm3, or 97.6%. In vacuum sintering, the achieved density is relatively high, because pore shrinkage is not hindered by internal gas pressure. While in reductive hydrogen atmosphere, the experimental density is 0.1% lower.
Tensile strength
The tensile strength of sintered stainless steel 316L can reach up to 587.0 MPa. However, it is evident that prealloyed feedstock provide higher tensile strength than master alloy. The main reasons of this difference are the residual carbon from carbonyl iron powder, or the contamination with element (Si, C, H, N) diffusion.
It is obvious that different powder types and sintering parameters have significant effect on tensile strength, while negligible effect on final hardness. The following picture are optical micrographs in both polished and etched conditions. It is obvious that master alloy has a finer grain size than pre-alloy, this results in the lower sintering temperature and less porosity.
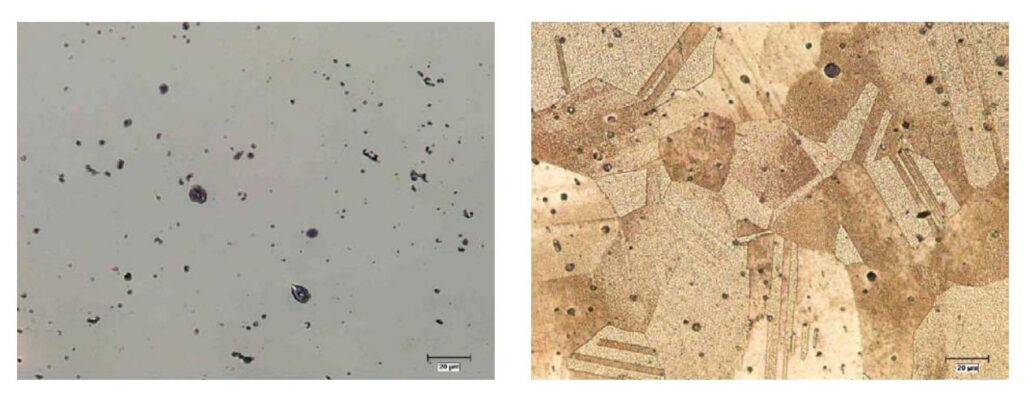

Addictive
B/Cu
The small additives of B and Cu will enhance densification, it will increase the final sintering density and improve the mechanical properties.
Zr
Zr is a stabilizing element in ferritic stainless steels, it can improve oxidation resistance at high temperature. It can inhibit the formation of Silicon oxide, its crystal grain refinement effect will suspect grains refinement in MIM 316L. In The MIM 316L sintering, the over growth of Si oxide in the grain boundary will inhibit densification, this leads to the degradation of mechanical properties and hardness. Once add Zr additive, the finely dispersed silicon oxide will act as the pinning agent. This will prevent the overgrowth of crystal grains, and refine the micro-structure of 316L parts.
All in all, the addition of Zr will contribute to resfinement of powder structure and inhibit the formation Si oxide on powder surface. Finally, improve the sintering characteristics and mechanical properties in MIM 316L sintering.
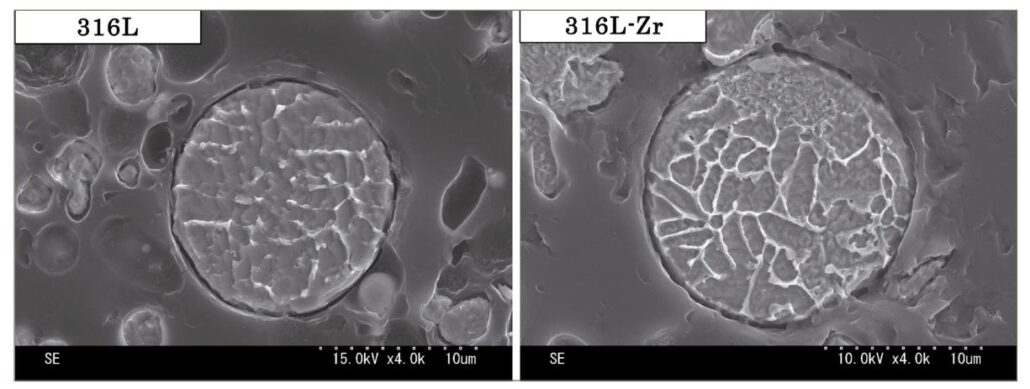
Delta Ferrite
In MIM 316L process, tensile ductility and axial fatigue strength will decrease as the content of delta ferrite increase. Otherwise, delta ferrite will also activate densificaiton, this will compensate these effects. The amount of delta ferrite increase with sintering temperature (over 1300℃), while decrease with the carbon content. In reason of carbon element stabilizes the austenite phase in stainless steel.
Sintering Atmosphere
The normal sintering atmosphere for MIM 316L are vacuum, H2 and N2.
H2 Atmosphere
Early 316L sintering experience indicates that H2 atmosphere is the optimum choice for low carbon stainless steel. As this will ensure the reduction of silicone and chromium oxides, which are stable even at high temperatures. Furthermore, there is no quality difference between sintered 316L parts in H2 and vacuum atmosphere. The following picture is micro-structure of phase distribution of 316L with low Ni content (10.4%). It is consisting of austenitic matrix with delta ferrite island (red arrows)
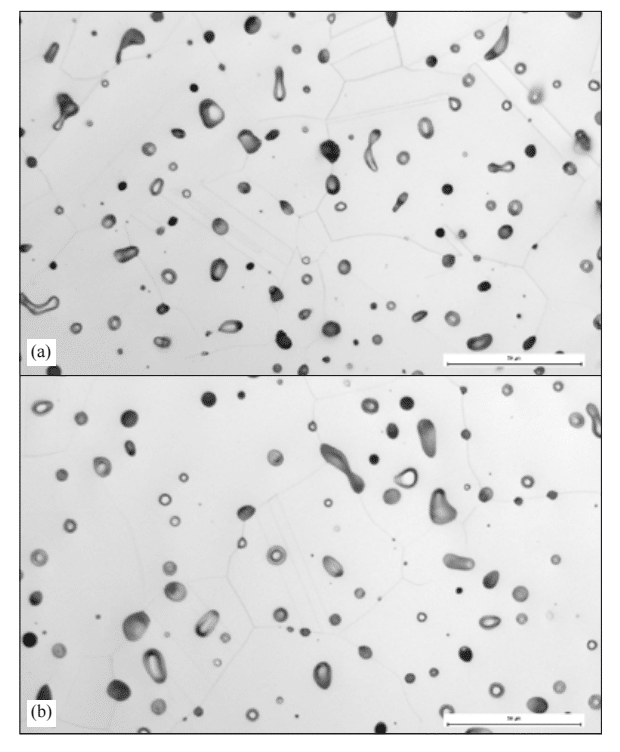
Once sinter 316L parts with high Ni content (13.5%) in H2 and vacuum atmosphere, the micro-structures exhibit a wholly austenitic as in the following picture. However, there are large number of visible pores, this results in the low theoretical density value of 95%.
N2 Atmosphere
Sintering in N2 results in nitrogen absorption, this will reduce density and improve yield strength. The fine powder with greatest surface area can absorb most nitrogen in sintering, this results in the highest strength with loss of some ductility.
For 316L parts sintered in N2 containing atmosphere, the visible phase is only austenite in micro-structure, even for the 316L with Low Ni (10.4%),(which is easy to form delta ferrite phase in sintering. Please check the micro-graph of 316L (Low Ni) in N2 sintering atmosphere.
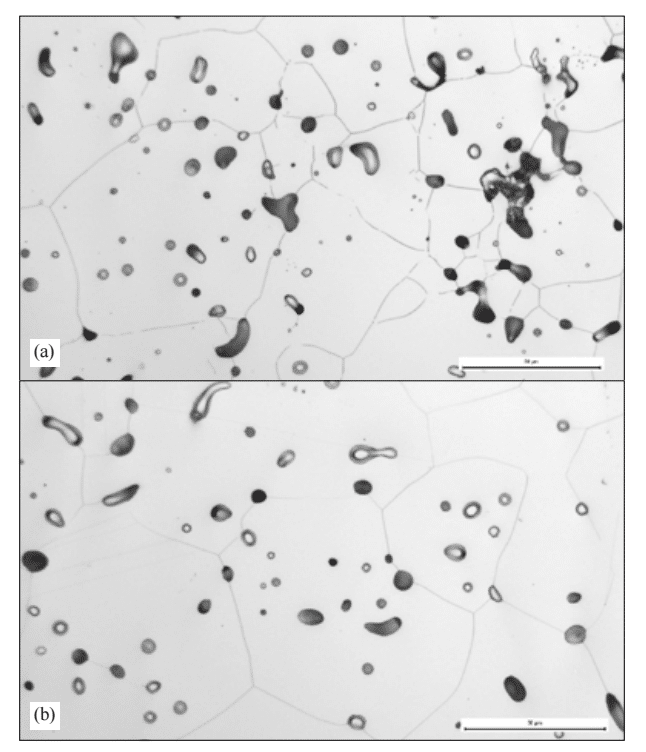
Sintering in N2 atmosphere provides the highest hardness value, as particle size of metal powder decreases, hardness increase. Nitrogen sintering also enhances stress by almost 100 MPa comparing to hydrogen sintering. Elongation results are influenced significantly by sintering atmosphere: H2 sintering achieve 70% elongation, while vacuum at 43% and N2 at 33% in average. The carbon content levels in vacuum and N2 are lower than H2, this suggests that carbon is the primary reductant for surface oxygen rather than hydrogen.
Conclusion
Stainless steel 316L provides top corrosion and abrasion resistance in harsh chloride environment. There is no doubt that MIM 316L provides a perfect balance between cost and efficiency.