MIM HK30
Introduction
HK30 is a niobium-stabilized austenitic chromium-nickel steel, it has excellent resistance to carburization, sulphidation, oxidation. This alloy is applied in high-temperature applications, especially in turbo chargers.
Normal Chemical Composition of MIM HK30
MIM HK30 | Iron | Carbon | Chromium | Nickel | Molybdenum | Silicon | Manganese | Niobium |
Percent by Weight | BaL. | 0.20-0.50 | 23.0-27.0 | 19.0-22.0 | 0.20-0.30 | 0.75-1.75 | 0.00-1.50 | 1.00-1.75 |
Mechanical Properties
Material | Density | Tensile Strength | Yield Strength(0.2%) | Hardness | Elongation(% in 25.4mm) |
MIM HK30 | ≥7.50g/cm³ | ≥700Mpa | ≥350Mpa | 150-220 HV1 | ≥35% |
In the automotive-engine category of MIM components, HK30 alloy is applied for the vane lever in the turbocharge of internal combustion engines. HK30 as the austenitic stainless steel, has excellent oxidation resistance and strength in operation temperature of 800 – 850℃. In previous case, this part is made by machining wrought bar stock.
HK30 in MIM
Metal injection molding is adopted for the production of various high temperature turbocharger components, this method displace precision casting or machining processes successfully. These turbocharge components require characteristics of high temperature wear&corrosion resistance, excellent fatigue properties. HK30 (AISI 310) is the most common alloy for manufacture of turbocharger vanes.
Since the control of carbon level and distribution is critical for final grain-size and properties. We need to well understand the HK30 powder characteristics and processing parameters. Including:
- Particle size distribution and chemistry
- Final density and metallurgical properties
- Effect of sintering temperature & atmosphere
In automotive industry, there are same metal parts need to resist erosion and corrosion from high temperature. These alloys should have excellent hot-wear and corrosion resistance, as well as good high temperature fatigue and creep strength, microstructural stability at operating temperatures. Such as for diesel engines, the temperature will reach to 850℃.
Critical Element in HK30
HK 30, as a heat resistant stainless steels, provides an excellent combination of hot strength, corrosion resistance, creep/fatigue life. It has featuring Nb addition for strengthening purpose, and Si addition to increase resistance to carburisation. Si is limited under 2%, in order to eliminate the long-term embrittlement in prolonged exposure to high temperature.
Carbon level controlling is critical to achieve required strength level, the grain size is desirable for strength and toughness optimization. High Cr and Ni content confer excellent resistance to hot corrosion, even in sulphur-bearing atmosphere.
HK30 Sintering Temperature
In 1300℃ sintering, HK30 alloy provide a higher density than 1280℃, the theoretical density will increase 3-4%. The increased density results in higher strength and ductility. However, the grain and carbide coarsening will moderate the observed increases.
Moreover, at 1300 ℃ sintering temperature, the grain refining agents can achieve grain refinement of prealloy without sacrificing densification or mechanical properties.
Sintering Atmosphere
Nitrogen and Argon are two most common sintering atmosphere in MIM HK30 process. These two different atmospheres result in different effects on the densification, microstructure, mechanical properties. In N2 sintering process, the N atoms dissolved into the austenite matrix, others combine with metal atoms, and precipitate along the grain boundaries. Therefore, this results in the higher hardness, the hardness decreases with the distance from edge to center. In addition, the sintered parts in N2 also have higher tensile strength than that in Ar.
HK30 Sintering
The most critical factor in MIM sintering is the atmosphere, it can determine density, micro-structure, multiple properties. Nitrogen is a strong austenite stabilizer, it can affect the final properties of HK30 parts significantly. The additional of nitrogen will increase the HK30 strength, hardness, wear-resistance, corrosion resistance.
Densification
The sintered density in nitrogen and argon are 7.48 g/cm3 and 7.62 g/cm3 respectively. Under the same conditions of 1280℃ sintering, the density of N2 sintering is lower than in Ar. The N content in Ar sintered parts is 0.05%, while 0.18% in N2 sintered samples.
In sintering process, nitrogen will enter into the steel and form nitrides, this will slow down the densificaiton rate by hindering the diffusion of iron or chromium. In addition, more H2O or O2 in N2, will result in the oxide layer during sintering. These oxide films also hinder the diffusion and formation of sintered neck. Therefore, the density in N2 is lower than that in Ar.
Micro-structure
In Ar sintering atmosphere, there is a homogeneous micro-structure, the grain boundaries are thin and smooth.
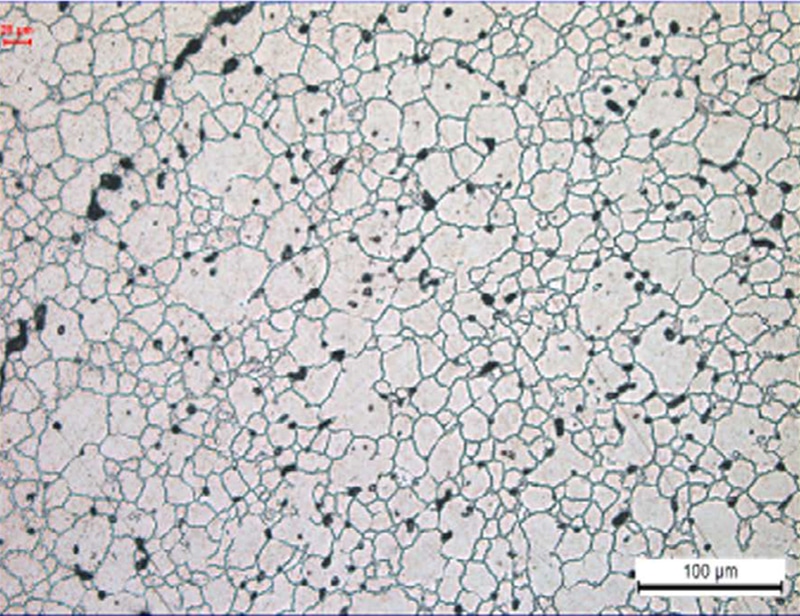
Microstructure Ar sintering
But in N2, there are a large volume of pores, and there are some needle-like phase precipitated at the edge region.
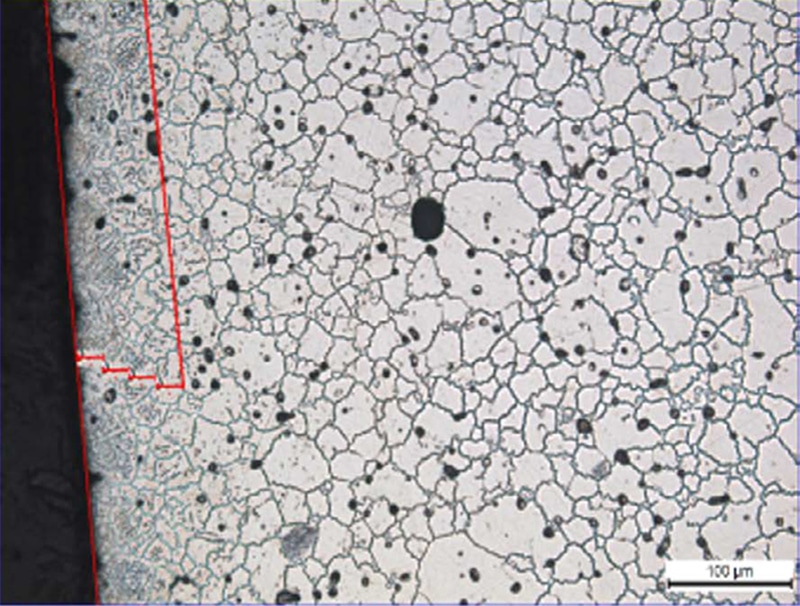
Microstructure N2 sintering
The surface distribution of nitrogen element in HK30 alloy. Some N atoms are dissolved in austenite, other s are accumulated at the grain boundaries.
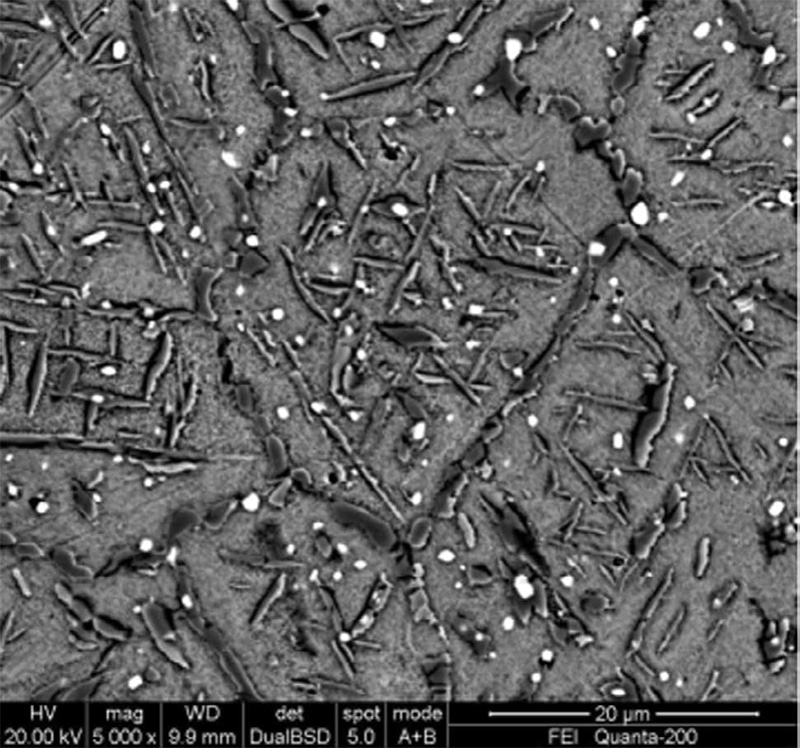
SEM image in N2
Mechanical Properties
In 1300℃ sintering, HK30 alloy provide a higher density than 1280℃, the theoretical density will increase 3-4%. The increased density results in higher strength and ductility. However, the grain and carbide coarsening will moderate the observed increases.
Moreover, at 1300 ℃ sintering temperature, the grain refining agents can achieve grain refinement of prealloy without sacrificing densification or mechanical properties.
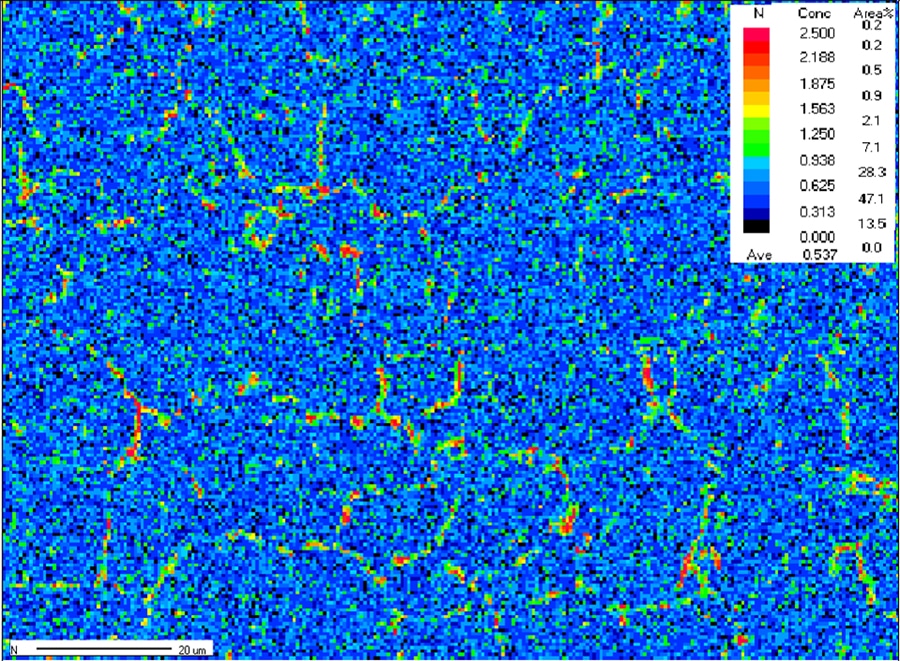
N distribution in N2
HK 30 Heat Treatment
HIP Treatment
HIP (Hot Isostatic Pressing) has significant effect on micro-structure and mechanical properties of MIM HK30. HIP can improve the tensile strength from 609.6 MPa to 645.0 MPa, elongation from 32.7% to 43.7%. All these improvement are attributed to fewer macro cracks, denser structures and finer distribution of Nb based carbide in the additional HIP processing.
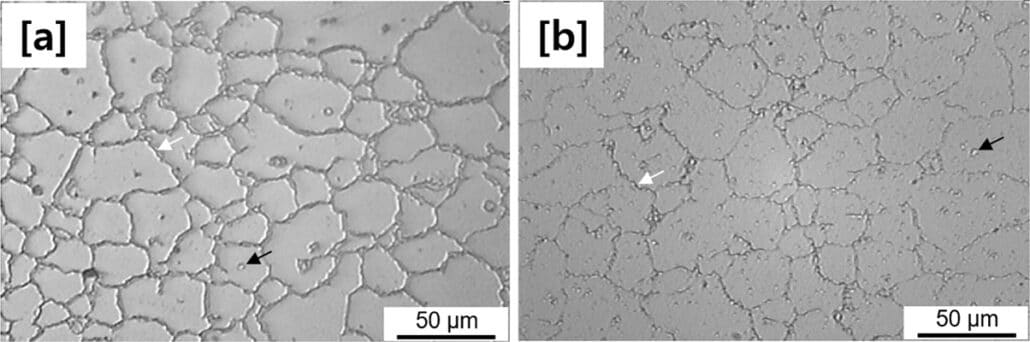
Optical micrograph MIM vs HIP
Solution Annealing
The micro-structure of HK is an austenitic matrix, there are large carbides along the boundaries of the primary grains. In order to eliminate the unfavorable trans-crystalline carbide network, solution annealing is applied improve ductility, creep resistance, and corrosion resistance.
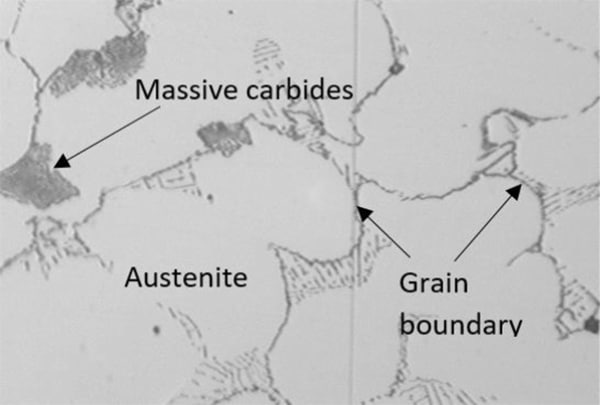
Sintered HK30
From the micro-structure after solution annealing , there are finer grains, and the carbides dissolute along the austenitic grain boundaries.
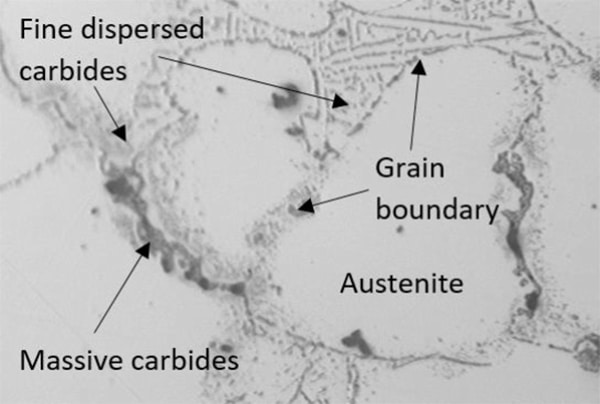
Solution Annealing of HK30
The solution annealing can bread down the coarse dendritic network of carbides, transfer the primary carbide into the solid austentic solution. Therefore, with the proper combination of heat treatment, it is possible to achieve the good hardness with an elevated toughness.
Conclusion
HK30 has excellent mechanical properties, fatigue and corrosion resistance, it is applied widely in automotive industry. ZCMIM has more than 15 years experience in HK30 MIM projects. Contact us for your next HK30 case.