Hot Isostatic Pressing
Hot Isostatic Pressing (HIP) is a critical post-processing technology for the Metal Injection Molding (MIM) industry. HIP is able to remove residual porosity in MIM components, in order to satisfy performance specifications and high-performance applications in automotive and aerospace industry. In addition, HIP is also common for aesthetic applications, reduction of porosity provides higher polishability.
Although Metal Injection Molding can achieve significantly higher density than Powder Metallurgy. There are still some requirements of full density MIM parts, Hot Isostatic Pressing (HIP) can achieve full density MIM parts, in order to improve mechanical properties, and ensure higher surface finish of machining, polishing and electroplating applications. Therefore, once apply HIP process for MIM parts, there are a number of factors to consider.
Hot Isostatic Pressing is an effective technology to achieve full density and improve mechanical properties for various MIM materials. It becomes an important finishing process for Metal Injection Molding.
- The HIP process can eliminate the remaining residual porosity in sintered MIM components. This results in superior material properties, such as enhanced fatigue strength, ductility and fracture toughness.
- HIP is also applied to achieve high-quality machined and polished surface for MIM parts. Since there is no residual porosity to reveal on surfaces in the subtrative (machining & polishing) process.
Hot Isostatic Pressing Process
Hot Isostatic Pressing (HIP) is a process to densify cast and sintered metal parts. It normally applies high gas pressure (50-200Mpa) and high temperature(900-2000℃) for steels and super-alloys. In HIP process, the gas pressure takes effect uniformly in each direction, results in 100% desification and isotropic properties. Argon is the most common gas pressure medium.
It is very complementary to metal injection molding and powder metallurgy (PM) process, or new additive manufacturing technologies (3D printing).
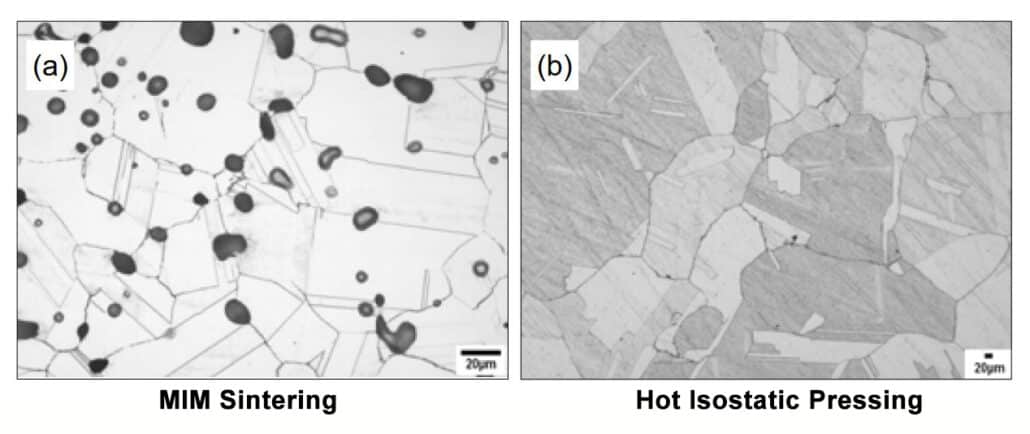
HIP Processing Steps
In this process, temperature, argon-gas pressure, holding time will vary depending on material types, part size, total quantity.
After plating MIM parts in the HIP vessel, the air is evacuated and argon gas is inflated. Then heating the HIP vessel to increase temperature, at the same time, argon gas pressure is also increasing in the vessel. Once reaching the calculated pressure, increase the argon pressure through gas thermal expansion. Keep the constant gas pressure and temperature in the holding time. Then take a rapid cooling process with decreasing pressure and temperature.
HIP Processing Parameters
In HIP processing, we should consider different parameters, in order to ensure the success. The cycle time of HIP is from 8 hours up to 24 hours.
- The heating temperatures are normally below 0.8 time of T solidus, in order to avoid liquid phase.
- The normal gas is argon, but other inert gases or gas mixture is available.
- The compressor is applied to rise up pressure in HIP vessel.
- The gas pressure is equal both inside and outside the insulation.
Uniform Rapid Cooling
In modern HIP systems, uniform rapid cooling (URC) can circulate lower temperature gas, and cool parts at the controllable rate of up to 100℃/min. Therefore, this HIP quenching technique reduce cycle time dramatically by shorten 80% time in the cooling stage. This technology also combines heat treatment and HIP in one step. The uniform rapid cooling process will restrict grain growth and thermal distortion of MIM parts, and avoid surface contamination by high purity argon gas.
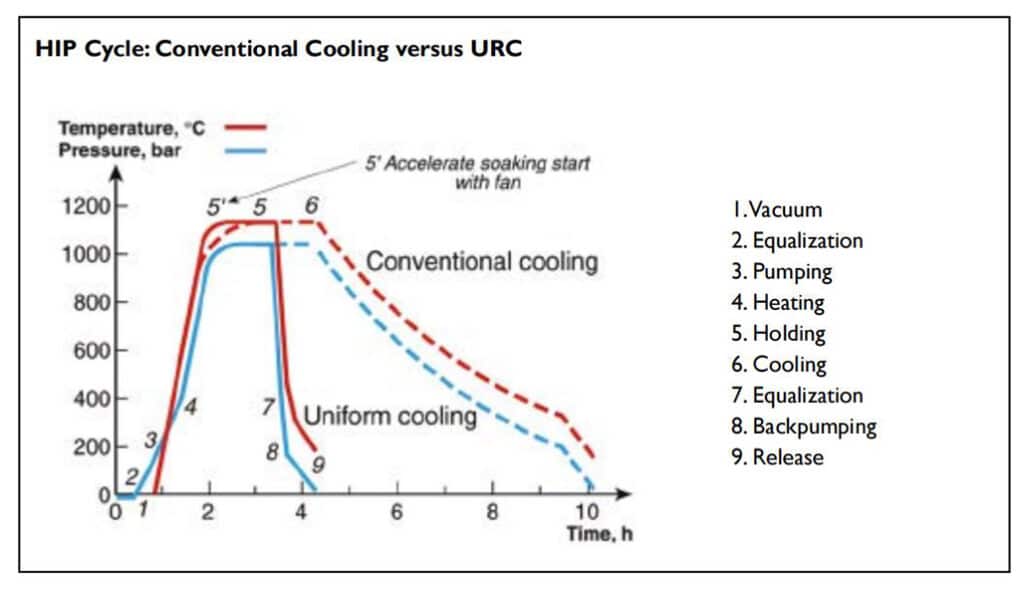
Hot Isostatic Pressing Facilities
The hot isostatic pressing (HIP) unit is normally consisting of a pressure vessel, a heating system and an argon gas system. While different HIP constructions are available:
- Frame construction for pressure above 100MPa and HIP diameters above 900 mm in safety reasons.
- Top screw thread locking system.
- Various heating system.
Molybdenum furnaces are suitable for temperatures up to 1350℃, while carbon graphite/tungsten furnaces are suitable for temperature up to 2000℃. In the HIP pressure vessel, insulation of ceramic fibers and Molybdenum sheets can protect the steel vessel against the heat, and hold the temperature inside the insulation. The bottom, cover and pressure vessel are water cooling, in order to protect the sealing and vessel against the heat.
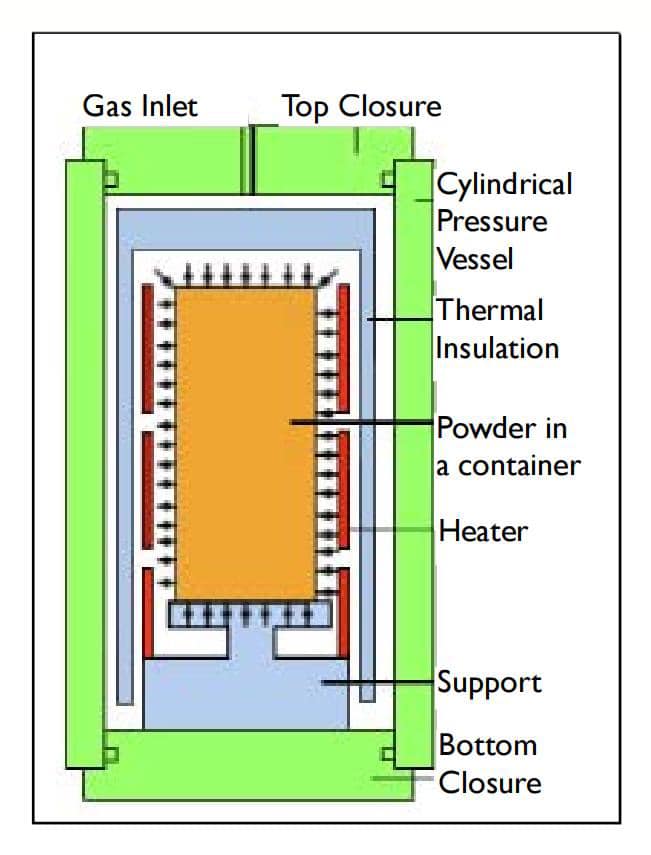
HIP Design Guidelines
The HIP design guidelines provide some hints regarding design and manufacturing, in order to understand the possibilities and issues specific to HIP technology.
HIP Component Shape
Once considering the HIP technology, there are four different options:
- Simple shapes like round, tubular, or flat bar.
- Near net-shapes to eliminate further machining or welding.
- Complex net-shapes to eliminate machining in functional area
- Bi-metal or composite construction with HIPing powder layer for functional area.
Computer Modeling
Computer modeling is an effective method to simulate accurately powder densification and shrinkage behavior. HIP engineers combine computer modeling and with the excellent experiences to achieve the optimum geometry and dimensions for final MIM parts.
Computer modeling also can optimize the HIP process for complex geometries, in order to eliminate expensive machining operations or avoid under-size risk.
Computer modeling is very useful for particular features, such as sharp corners, thickness variant.
HIP Container Parameters
HIP container is the most critical facility in HIP process, there are several parameters we need to consider in process.
Mold-media Interfaces
Container materials and thickness are very critical parameters in HIP process for MIM parts. Normally, the container must satisfy the considerations as following:
- Containers must be strong enough to maintain shape and dimensional during HIP.
- It must be leak proof at both low and high temperature.
- It is weldable for sealing and removable after HIP.
- Containers must be compatible with the MIM parts, not penetrate nor react with MIM parts.
The most common container materials are low carbon steel or stainless steel. In specific cases, high temperature materials are applied, such as titanium or super alloys.
Container Shrinkage
During Hot Isostatic Pressing, there are many factors to affect the isotropic shrinkage of container, like: container materials, overall geometry, thickness, welding position.
Micro-Structure In HIP
Hot Isostatic Pressing (HIP) combines with Metal Injection Molding (MIM) for complex MIM part densificaiton.
Porosity Elimination
In HIP process, MIM materials are heated to required level, where the flow stress of alloys decrease and diffusion become active. Then apply hydrostatic pressure to drive densification by plastic flow of metal and mechanism of diffusional creep.
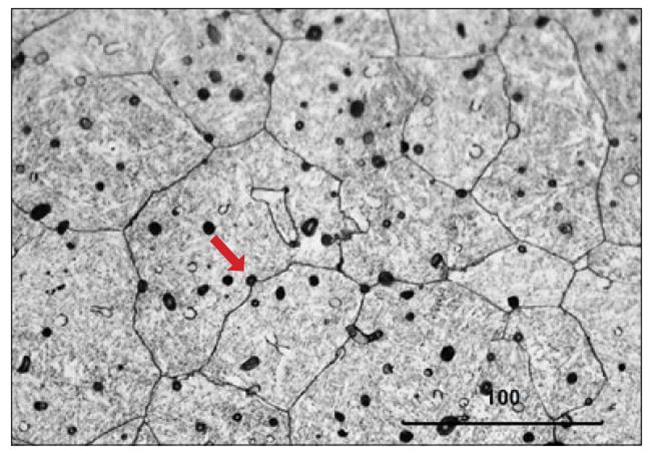
Prior to HIP, MIM components should be sintered into a point with all pores are isolated from the metal surface. Then HIP technology can eliminate these sub-surface pores (in following picture)completely. There is shape and dimension change in HIP process, the total volumetric shrinkage is equal to the fraction volume of porosity. Localized deformation will result in dimples on the surface, this means metal has flowed into the near-surface pores.
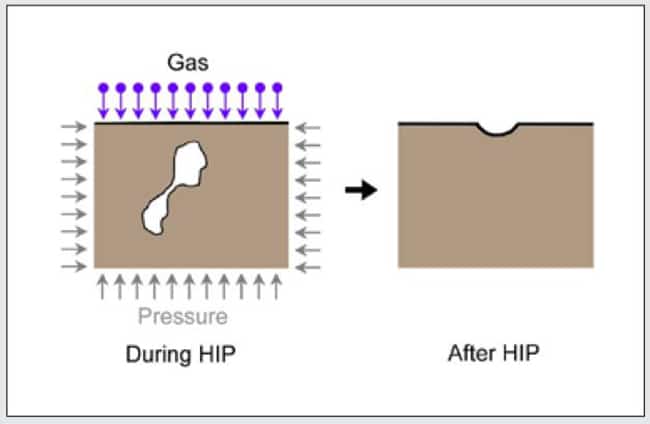
From the micro-structure of MIM 420 stainless steel after sintering, many pores are isolated within the grain after high temperature sintering. However, there are still pores pin on the current grain boundaries, and become isolated as the boundary breaks free. This area won’t consolidate into pore-free level in HIP cycle. The surface-connected pores (as following picture) are unable to remove in conventional HIP cycle.
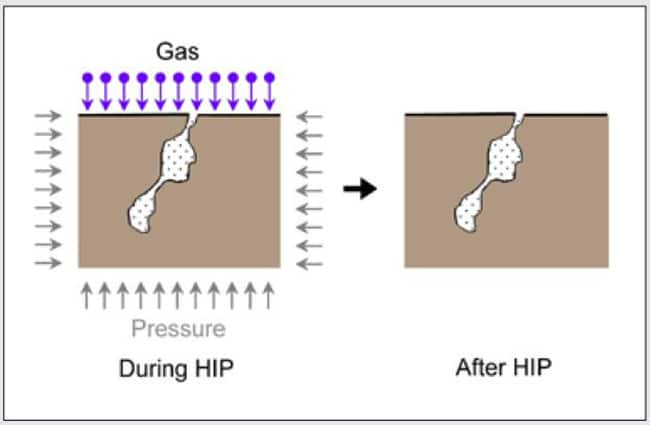
Grain Growth in HIP
In Metal injection molding process, high sintering temperature can decrease pore fractions, then achieve higher density. However, the grain growth in high temperature sintering is an issue for diffusional densification in HIP.
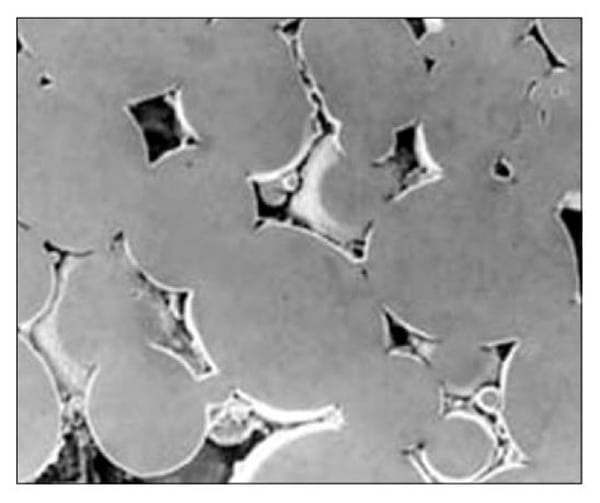
The densification process in HIP relies on diffusion, specific in atom transportation to pore surface, and atomic vacancy movement to part surface. In initial HIP stage, the collapsed particle surface fuse and become grain boundaries. Since MIM products apply finer metal powder than PM, MIM materials have a higher driving force for grain growth. In this case, we need to avoid over sintering (see MIM 420 stainless steel graph) once require further HIP process. Otherwise, conventional HIP cycle is difficult to eliminate these pores.
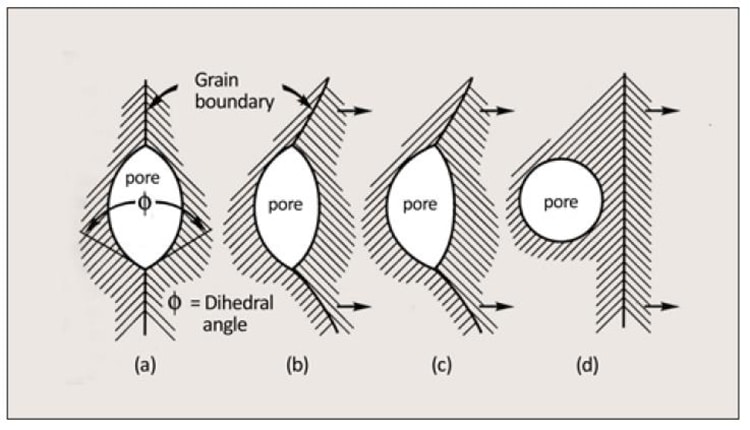
HIP Benefits
HIP provides many benefits, it is a viable and high-performance alternative to conventional processes, like: forging, casting, and machining.
Hot isostatic pressing is a common post-sintering process for MIM parts. It can eliminate the residual porosity in MIM parts. HIP combining with MIM technology results in significantly advantages.
Improve Mechanical Properties
The residual porosity has significant effect on the final mechanical properties, the following graph illustrates the effect on tensile strength, ductility (percent elongation), impact resistance.
The improvement with HIP for ultimate tensile strength is estimated at 4%, the ductility increase at 10% in prediction, and the impact resistance will improve almost 40%. In addition, high cycle fatigue life is another property, like impact toughness. This is very sensitive to the residual porosity.
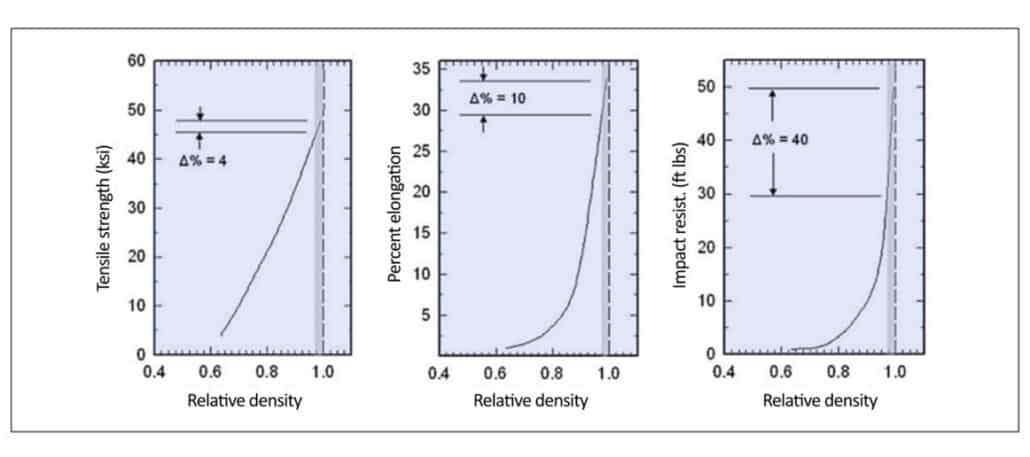
Therefore, once MIM parts are processed after HIP, the improvement in ductility is significant, while tensile and yield strength are negligible or non-existent.
The significant improvements of HIP are impact resistance, fracture toughness and high cycle fatigue. Elimination of the last porosity percent will lead to dramatic improvement of MIM parts. However, residual porosity is only one of several micro-structural defects in MIM products. Other factors like oxides, sulfides, silicates have detrimental effect on mechanical properties similar to porosity. These defects will limit or eliminate any improvement by HIP.
High Appearance Finish
High polishing surface is required for functional reason in MIM parts. However, sub-surface porosity is a critical defect during polishing operation. Metal injection molding is suitable for manufacturing of jewelries and decorative items. For mirror-like polishing appearance, any fine porosity become visible will result in unqualification. In addition, electroplating and electron-polishing are also undertaken for functional or aesthetic reason. In these processes, near-surface porosity results in significant defects, highly polished surface will make any small and tiny defects more visible.
In order to achieve high appearance finish from polishing, electroplating and electron-polishing. HIP is a cost-effective method to improve surface quality of MIM parts
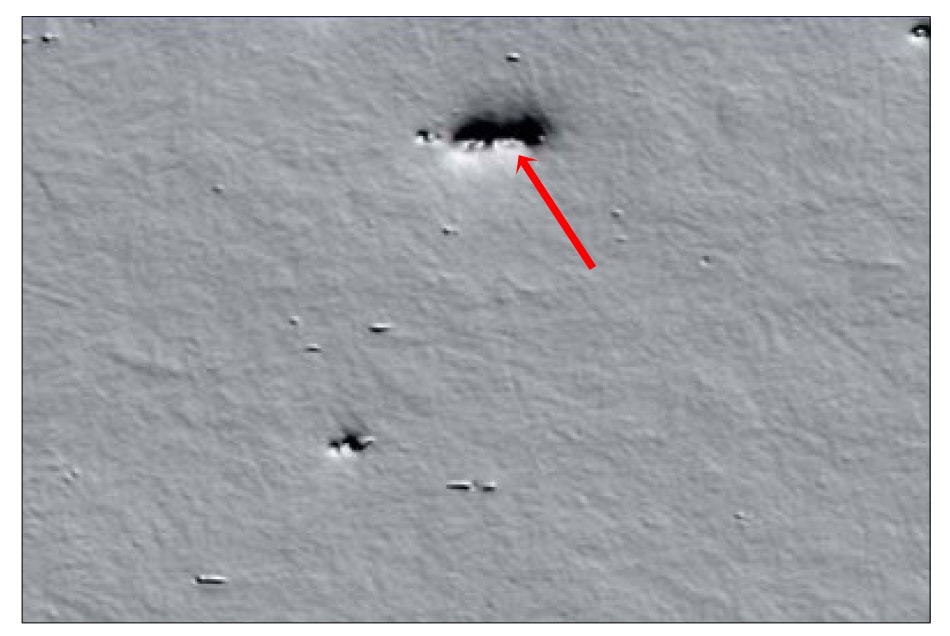
Infection Preventing in Medical
MIM technology is popular for medical industry, especially for surgery and dental components. In medical applications, any sub-surface porosity is harbors for bacteria. These defects are easily created in during machining and finishing operations. Therefore, HIP is a reasonable process to eliminate the risk of infection in operating room. Even there is no mechanical property specifications.
Conclusion
The Main benefits of HIP technology for Metal Injection Molding:
Component Quality and Performance
- Fine and isotropic micro-structure
- Elimination of welding on complex parts
- High density without segregation
Design Flexibility
- Net shape or bi-metal construction
- Composite materials
- Free part sizes and production series
- Free alloy options
Cost Reduction
- Shorter production leading time
- Eliminate further operations
- One single part consolidation