Metal Injection Molding vs 3D Printing
Metal injection molding (MIM) vs Metal 3D printing (Addictive Manufacturing) are high competitive metal manufacturing technologies. These two metalworking methods are cost-effective for small and complex metal parts production. Otherwise, these two metal manufacturing methods have unique benefits and limitations.
Metal Injection Molding(MIM)
Metal injection molding is a core metalworking technology for small components’ production with various material options. MIM operations have reliable capability of high-volume production and excellent material properties.
MIM is suitable for components in numerous industries like medical, automotive, electronic and general industrial. In reason of large investment in MIM tooling, once amortized over millions of units, it is also reasonable to apply MIM technology in economical aspect.
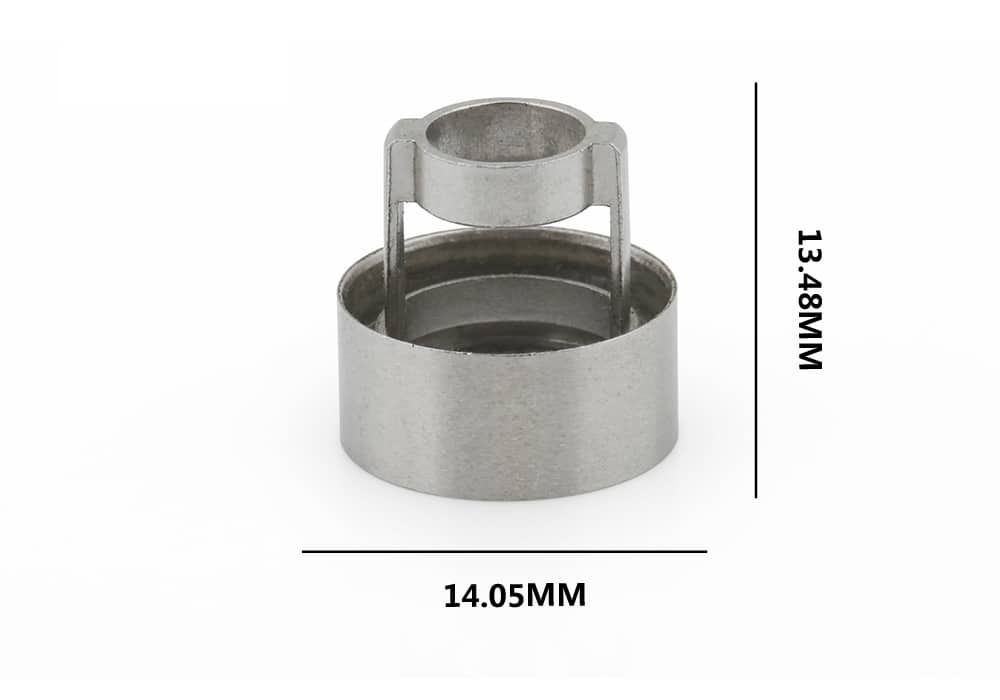
MIM Process
Metal injection molding (MIM) technology combines plastic injection molding with powder metallurgy, in order to create net-metal parts with complex geometries. This MIM process including four main stages – feedstock compounding, injection molding, debinding and sintering.
- Fine metal powders combines with thermoplastic material and wax binders, then granulate into small pellets – Feedstock.
- These feedstocks are heated and injected in normal injection molding machines, then create required shapes in different mold cavities – Green Parts.
- After molding, the binder materials will be removed from molded parts in debinding furnace, resulting in a – Brown Parts.
- The brown parts are moved into sintering furnace, then heated to a relatively low temperature to burn out remaining binder. At last, these parts are sintered at high temperature near the melting point of the metal, and density to the final – Sintered parts.
MIM Applications
Engineers select MIM technology to produce small parts with complex structure particularly, these parts are difficult to manufacture effectively by other metalworking process. Since we can only one mold in the whole MIM manufacturing process, it guarantees the high repeatable and yields parts are uniform, shape and strength.
MIM parts have wide application in major commercial and industrial sectors, from automotive, electronics to medical, aerospace.
MIM Benefits
Metal injection molding is an effective method for high volume production. The finished MIM parts have smoothness surface finish with relative strength. MIM technology is compatible with a wide range of metal materials, these are mostly steel. MIM materials are in powder form and suitable for sintering.
MIM Limitations
As MIM technology requires the precise molds to produce MIM parts, it comes with numerous limitations. MIM molds will cost $5,000 to $10,000 in average, this is prohibitively expensive for low-volume production. Normally, MIM only makes finical sense for annual production over 50,000 with long-term production life-cycle.
Furthermore, we need to consider various design challenges MIM designing process. Mold designs are difficult to alternated and there are still significant limitation is shape. Such as:
- Large overhangs should be eliminated, because it needs to be ejected from the cavity.
- Wall thickness is another design challenge in debinding process. Too thick walls are difficult to debind, while too thin walls are easy to collapse.
Metal 3D printing
Metal 3D printing technology including two typical method: Metal Powder Bed Fusion and Metal Binder Jetting(MBJ). Normally, Metal Powder Bed Fusion including: SLM (Selective Laser Melting), DMLS (Direct Metal Laser Sintering), EBM (Electron Beam Melting).
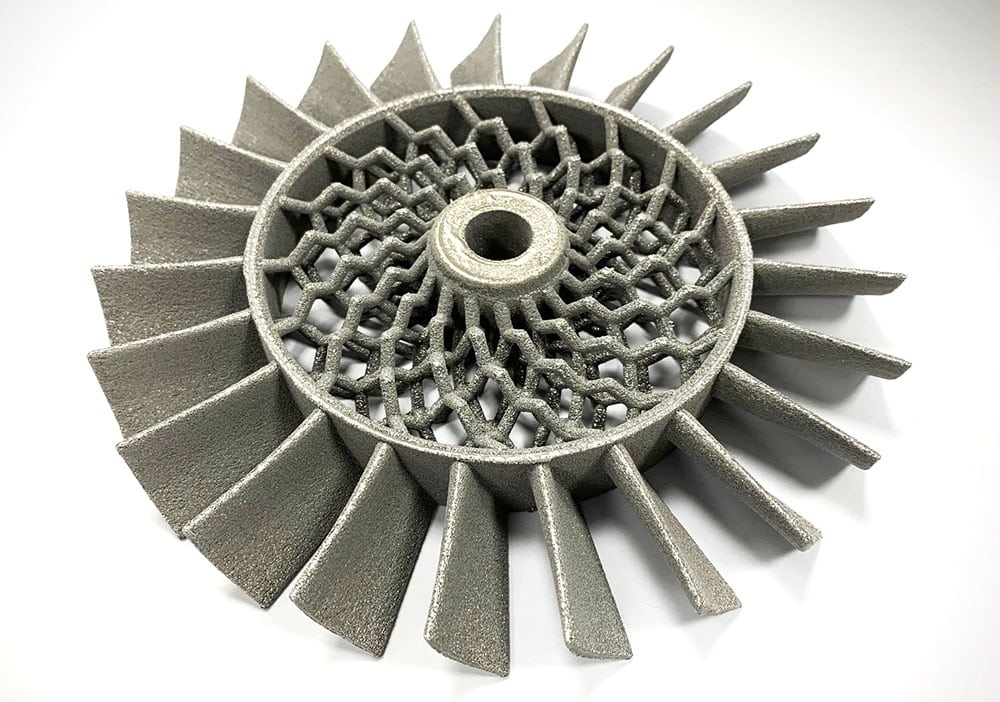
Metal 3D Printing Process
Although metal 3D printing has different methods, the common process is apply high energy method to produce parts from metal powder.
In this process, the inert gas is prepped in the chamber to minimize oxidation in melting or sintering. At first, a thin layer of metal powder is spread on the build platform, then the laser system will melt the powder together in small sections. After that, repeat these powder spreading and melting steps until the final part is fully built. Once the part cools, excess metal powder is removed. The part is stress-relieved and detached from the build plate, and heat-treated as requirement.
Metal 3D Printing Applications
Powder bed fusion processes are ideal for industrial applications with high-performance engineering requirements. Common applying cases are jet engines, medical equipment, turbine blades, and powder generators. Therefore, these 3D printing methods are compatible with more and more metal alloys, even precious metals like gold and platinum.
There are other metal 3D printing methods, like metal binder jetting and metal extrusion. Which are better suited for applications with fewer regulations and critical performance.
Metal 3D Printing Benefits
Metal 3D printing is specialized in metal parts with specific properties, such as high strength and durability, chemical resistance, unique design features. It provides more design freedom for engineers. As molds are eliminated, it is easy to update the design in computers. Any complex design will never contribute to additional production cost.
Metal 3D Printing Limitations
Metal 3D printing has its own challenges, its building size is limited by the strict manufacturing conditions and process controlling. The cost of an industrial-grade 3D printing machine is millions, this doesn’t include the cost of materials.
Comparison between MIM and Metal 3D Printing
Metal Injection Molding (MIM) and Metal 3D Printing have the similar production capability of durable and high-quality metal components. Both technologies provide device manufacturers (DMs) and their contact manufacturers(CMs) an alternative to traditional methods of machining, die casting, investment casting, powder metallurgy.
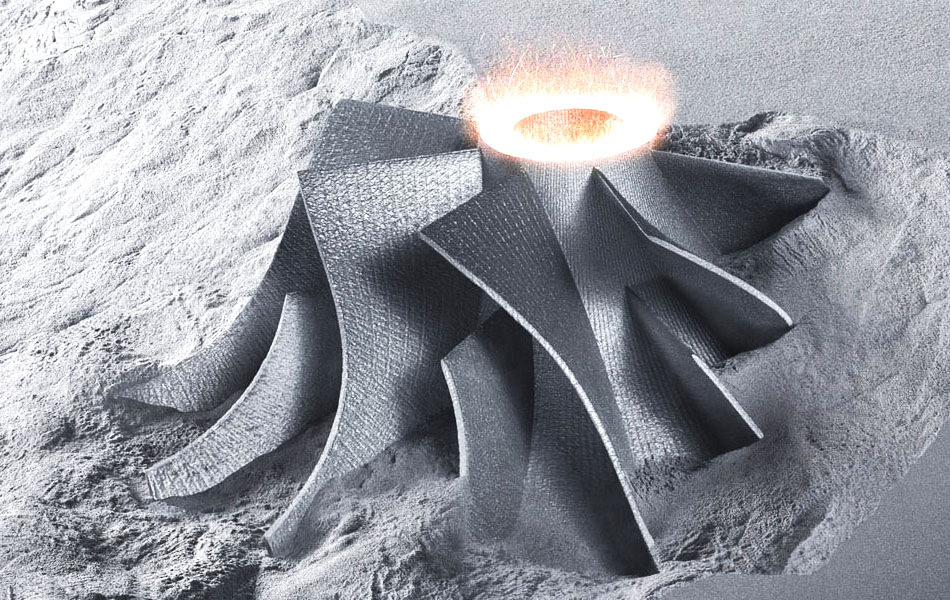
Freedom From Mold
MIM is always the choice for high volume production of small and complex components. However, the high-cost tooling is the key element to limit MIM technology. Furthermore, any feature change in MIM design will result in further mold modification. This also give rise to additional cost.
Metal 3D printing eliminates the requirement of tooling, but it’s cost per part are still very high. Such as a DMLS machine will cost over a million dollars, materials will cost as much as $330 per kilogram.
Unlimited Design Freedom
Metal injection molding requires a mold to create the green parts, there are more geometry limitations than metal 3D printing. The MIM mold is great for a highly automated process, this makes sure high volume production in molding process.
On the other hand, metal 3D printing build parts on a layer-by-layer basis, this means any new design is possible. Furthermore, additional complexity never results in additional mold and production cost.
Low Cost Competition
Although Metal 3D Printing has no limitations in geometry design and mold tooling, its high energy consumption and machine investment result in extremely high cost-per-part. Comparing to metal injection molding, normal metal 3D printing methods: SLM, DMLS and EBM, have no price advantages. In this case, common metal 3D printing are only suitable for low volume metal parts with complex geometry, which is difficult to create by injection molding method.
Comparison Table
Metal Injection Molding | Metal 3D Printing |
40 years technology | 20 years technology |
Best production of more than 20,000/year | Best production of less than 20,000/year |
$5k-10k mold cost | No mold require |
Single component per mold | No additional cost for update |
Limited geometry | Design freedom |
Best for part design without change | Best for part design with frequent modification |
Higher tolerance with stable production | Normal tolerance in production |
Metal Binder Jetting Difference
However, Metal binder jetting (BJT) is the new low-cost bind&sinter technology in metal 3D printing. This rapid-process method provides tool-free and high-volume production, which can leverage existing MIM expertise and equipment. As the development of metal binder jetting technology, it is becoming a great complement to metal injection molding. The cost of BJT is so low that it can compete directly with MIM.
Conclusion
Although Metal Binder Jetting (MBJ) drives down the price-per-part for metal 3D printing, it has less competitive advantages than metal injection molding (MIM). MBJ is a great option once production volumes are well above prototyping, but below the break-even cost of MIM tooling. Normally, once annual volume under 20,000 pieces, metal binder jetting is more cost-effective. Otherwise, MIM technology has no limitation in annual volume, high volume production will cut down unit price dramatically.
It is critical to notice the tolerance of metal parts in MIM manufacturing. Metal injection molding can provide more stable tolerance of ±0.3% in mass production, while MBJ only can provide nominal tolerance of ±0.5%. On the other hands, Metal binder jetting, as metal additive manufacturing, has higher design flexibility. It is able to create specific geometry, which is impossible with MIM.
In conclusion, ZCMIM is researching the most cost-effective method to manufacture small and complex metal parts. Our professional engineering team will finish the cost analysis quickly to determine the best option. If you have any requirement of metal part production, contact us now for professional advice.