Nickel-Free Stainless Steel
Metal injection molding (MIM) has the growing demand for nickel-free stainless steel in complex components, especially in application of watchmaking, luxury goods and medical devices. However, there are several challenges in MIM manufacturing process, ZCMIM engineering team review these challenges and share the insight of nickel-free stainless steel.
The common Ni-free stainless steel in our MIM production is PANACEA. It obtains non-magnetic, corrosion-resistant characteristics with excellent hardness and impressive polish-ability. This nickel-free stainless steel with high nitrogen content can satisfy high-requirement in luxury good and medical applications. Check the property data of PANACEA by the following button.
Stainless Steel Properties
Stainless steels provide the high corrosion resistance in various applications. This is the most significant characteristic of stainless steels.
Comparing to standard steels, stainless steels have a passivization layer of chromium oxide(Cr2O3), which protects from corrosion. Chromium oxide is a stable and homogeneous oxide with coefficient of thermal expansion, this enables chromium oxide layer to have excellent adhesion to steel.
In addition, chromium oxide achieves a good surface appearance of satin or mirror polishing, and renews itself without any additional coating.
In reason of low ductility of stainless steels, these steels are difficult to machine or stamp. Rolling process with high strain hardening will result in catastrophic degradation of corrosion resistance. Furthermore, brazing and welding will modify the micro-structure and foster chromium carbide precipitation. This will also result in corrosion resistance degradation.
In this case, traditional manufacturing method is limited, particularly for small complex parts. Therefore, metal injection molding (MIM) is able to produce stainless steel parts with lower cost. Moreover, MIM technology enable consolidation of multiple components into one single part, this avoids the issue of brazing and welding.
Nickel Stainless Steel
Nickel is the common element in steel materials, the most common grades of stainless steel contain nickel. In reason of the chemical properties of nickel element, it results in two unfortunate drawbacks.
Allergic Reactions
The presence of nickel will cause allergic reactions in humans. Nickel alloys can release allergenic ions, these ions are easily absorbed by the contact skin. For a nickel-sensitive person, this will result in skin rashes of itching, redness, eczema.
Toughness and Ductility Increase
The addition of nickel element will increase the toughness, ductility and malleability of stainless steel. These nickel stainless steel parts are easily scratched in normal applications. Such as stainless steel 316L, it is a typical nickel stainless steel, only has hardness of 120-140 HV. The low hardness limits its functional application with friction resistance.
The presence of nickel element, therefore, limits the application of nickel-containing stainless steel. Particularly in medical sector of prostheses and implant, jewelry and watchmaking.
Nickel Functional Mechanism
Ferrite Micro-structure Formation
From the article of PANACEA sintering effect, there are two ferrite formation related to magnetic properties: austenite (γ-ferrite) and martensite (δ-ferrite). Besides, stainless steels still have another ferrite formation of α-ferrite, this form still has a body-centered cubic (BCC) crystal structure. The α-ferrite are more corrosion-sensitive than γ-ferrite, the presence of α-ferrite micro-structure in stainless steel will increase the softness and magnetic properties.
Nickel Function in Micro-structure
Stainless steel contains at least 10.5% chromium element to confer corrosion-resistance by the passivization layer formation of chromium oxide. However, chromium is alphagenic, it favors α-ferrite formation in stainless steel strongly. This will reduce hardness and increase magnet of stainless steel.
Therefore, Nickel (Ni), as a strong gammagenic character, is added in large quantities to obtain austenitic structure in stainless steel. Austenitic phase ferrite will not only increase hardness, but also provide paramagnetic properties.
Nickel Elimination from Stainless Steel
In order to remove nickel element from the ferrous matrix in stainless steel, it is necessary to replace the nickel absence by other gammagenic elements. Nickel -free stainless steels normally contain the elements of Fe-Cr-Mn-Mo-C-N.
Carbon (C)
Carbon has thirty times higher austenitic participation effect of than nickel at the equivalent concentration. It is also easy to increase carbon content by addition in alloy manufacturing process, and this addition process will not impact the cost. Nevertheless, it is infeasible to obtain austenitic micro-structure solely by increasing carbon content in stainless steel. Excessive carbon inclusion will result in precipitates formation (Chromium carbides, Cr23C6) at grain boundaries, these precipitates degrade corrosion resistance because of local chromium depletion. In addition, these chromium carbides will also reduce the polishing ability of concerned parts.
Nitrogen (N)
Nitrogen has almost eighteen times higher than nickel in austenitic formation effect. It is a volatile element in the steel, its concentration can be changed by surrounding atmosphere composition at high temperature. Therefore, we can modify nitrogen content of stainless steel in MIM sintering process. But we should limit nitrogen concentration to avoid chromium nitrides (Cr2N)precipitates.
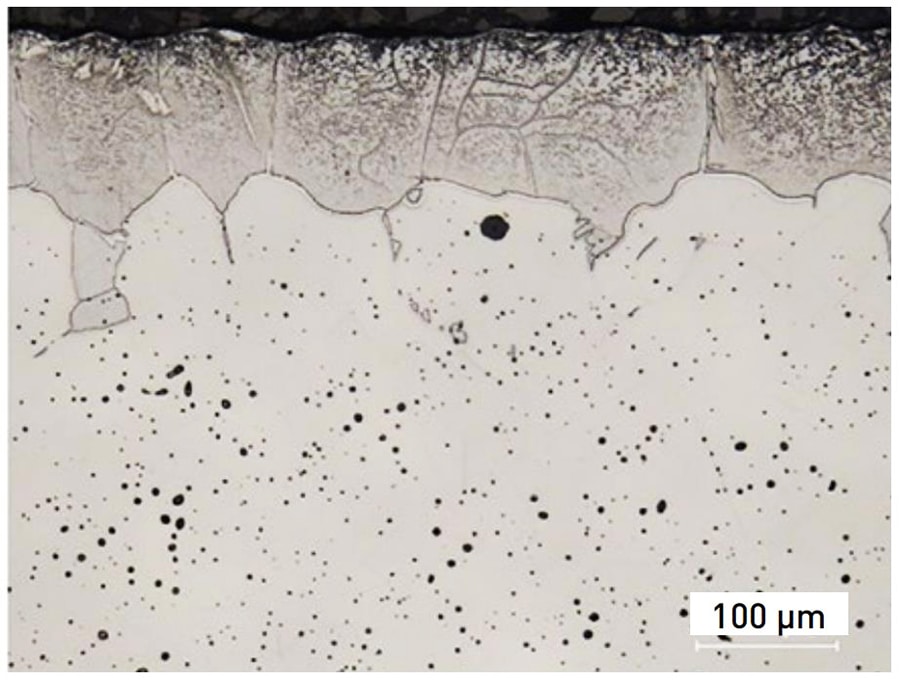
Manganese (Mn)
Manganese has a minimal impact on austenite formation, but increase the solubility rate of nitrogen strongly. Therefore, manganese presence affect the final micro-structure of steel indirectly. Although the addition of manganese improve machinability, it also has unfavorable effect on corrosion resistance.
Nickel-free Stainless Steel MIM Manufacturing
In MIM manufacturing process, it is critical to consider not just the alloy composition, but also micro-structure of final MIM parts. The micro-structure of nickel-free stainless steels determine the final mechanical properties and corrosion resistance. The sintering process and heat treatment will result in different micro-structure in stainless steel, this will completely change mechanical properties of MIM parts.
PANACEA is the most common nickel-free stainless steel in the MIM industry. ZCMIM apply the PANACEA from BASF (German) and ZDX (China), you can check the composition as following:
P.A.N.A.C.E.A. | Iron | Nickel | Molybdenum | Manganese | Carbon | Chromium | Nitrogen | Sulfur | Phosphorus |
Percent by Weight | Bla. | 0.0-0.1 | 3.0-3.5 | 10.0-12.0 | 0.0-0.2 | 16.5-17.5 | 0.75-0.90 | 0.00-0.03 | 0.00-0.045 |
Normally, there are no major differences between nickel-free stainless steel and nickel-containing stainless steel. The behavior of nickel-free steel are changed during sintering and heat treatment as the nickel-containing stainless steel.
Sintering of Nickel-free Stainless Steel
Sintering is the most critical step in MIM process, it transforms the bound metal powders into a dense and mechanical viable structure. From the cross-sectional view of sintered PANACEA in the following picture, there are nitride precipitates (Cr2N) formation on the surface. Moreover, the slow cooling process after sintering will increase the amount of α-ferrite.
Heat Treatment – Quenching
From the continuous cooling transformation (CCT) diagram for PANACEA. We can notice that heat treatment is necessary to obtain a complete austenitic structure by rapid cooling – quenching. The nitride layer will disappear and the α-ferrite is removed less than 1.5%. The quenching will also increase resilience to corrosion and surface hardness. For example, PANACEA parts after quenching have approximately 300HV surface hardness, while stainless steel 316L has 120 to 140 HV hardness without work hardening.
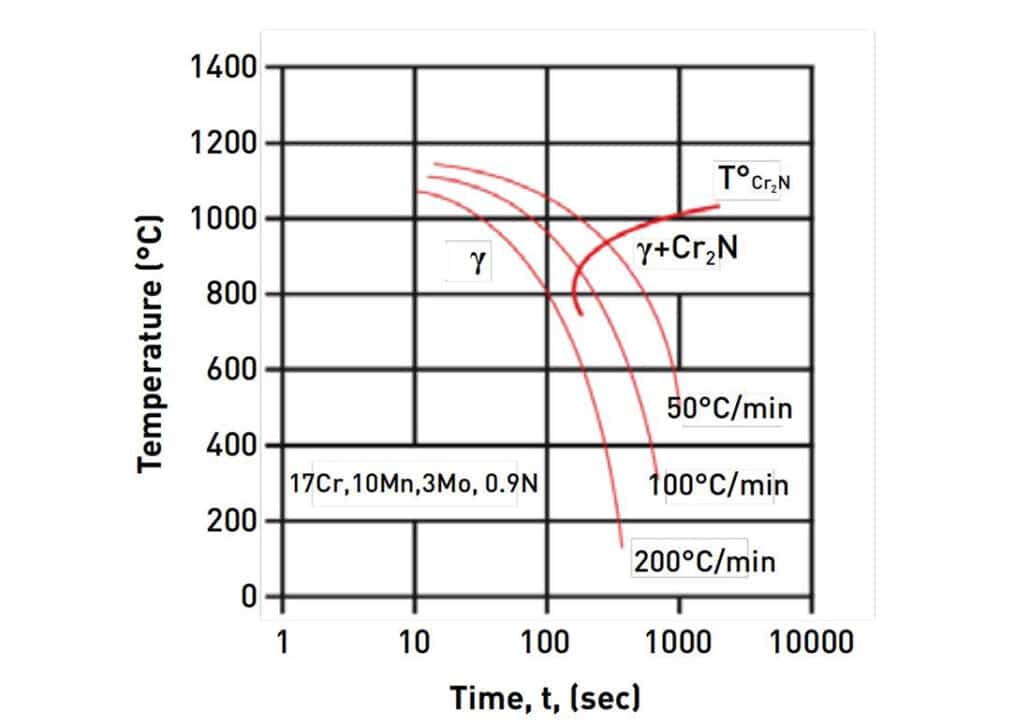
Polishing of PANACEA
After heat treatment, the surface of PANACEA parts have a dense microstructure without residual porosity. This dense layer is from the surface to a certain depth, therefore, the polishing of this layer result in an excellent aesthetic result.
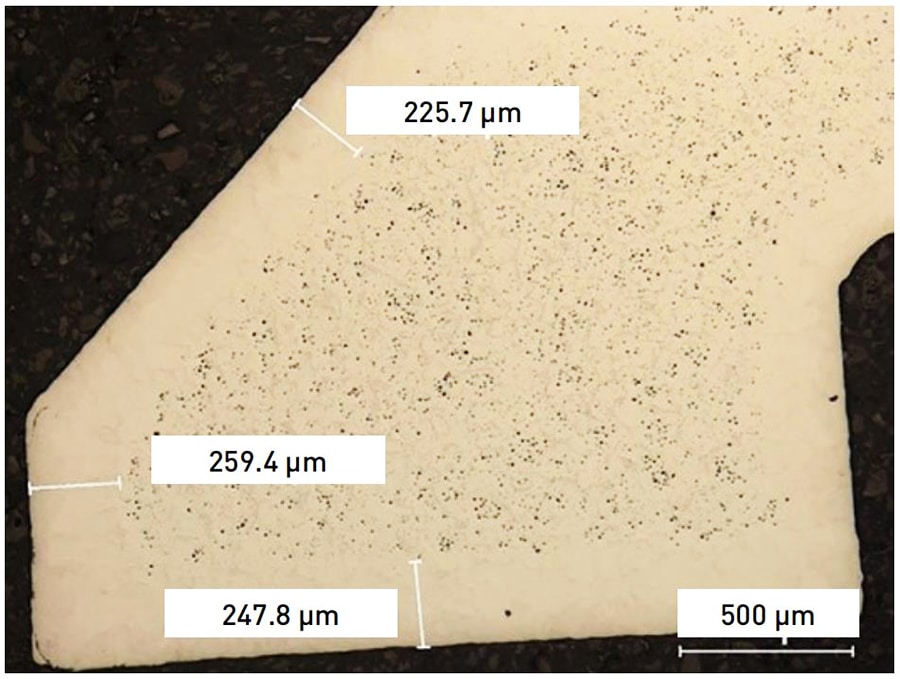
However, there is residual porosity from the certain depth. This substantial porosity is an issue for aesthetic parts. Once exaggerated polishing removes the dense layer and reveal the porous layer, there are visible pitting appearance on the surface, and the polish quality will decrease.
Conclusion
The application of standard stainless steels is popular in many industries. However, many applications are limited by nickel presence, particularly in terms of hardness and salting-out. PANACEA, as a common nickel-free stainless steel, obtains properties of non-magnetic, corrosion resistance, excellent hardness and impressive polish-ability. ZCMIM apply this specific material in high-requirement fields such as luxury parts or medical applications.