MIM 17-4
MIM 17-4 PH is a precipitation hardening grade of stainless steel with necessary high strength and hardness. Stainless steel 17-4 PH has better corrosion resistance than 400 series stainless steel, because of its low carbon content. Furthermore, modifying the aging temperature in heat treatment will achieve a wide range of properties and hardness.
A wide range of properties and hardness is able to achieve through heat treatment, this material is typical in medical applications.
MIM 17-4 PH Introduction
MIM 17-4 PH is a martensitic precipitation-hardening stainless steel based on the AISI 17-4 PH standard. It is characterized by combination of mechanical properties and corrosion resistance.
17-4 PH stainless steel is one of the most popular MIM materials in metal injection molding industry. This metal has excellent combination of strength, hardness and corrosion resistance. The excellent properties of 17-4 makes it possible to complex parts with good strength. In addition, the secondary hardening is also done in the sintering process with adjusting parameters.
17-4 PH has similar corrosion resistance to 304L, it is substituted in many application with mechanical requirements.
MIM-17-4 PH also carries identifications like: Stainless steel 17-4 PH, UNS S17400, AISI 630, ASTM A564, and AMS 5643.
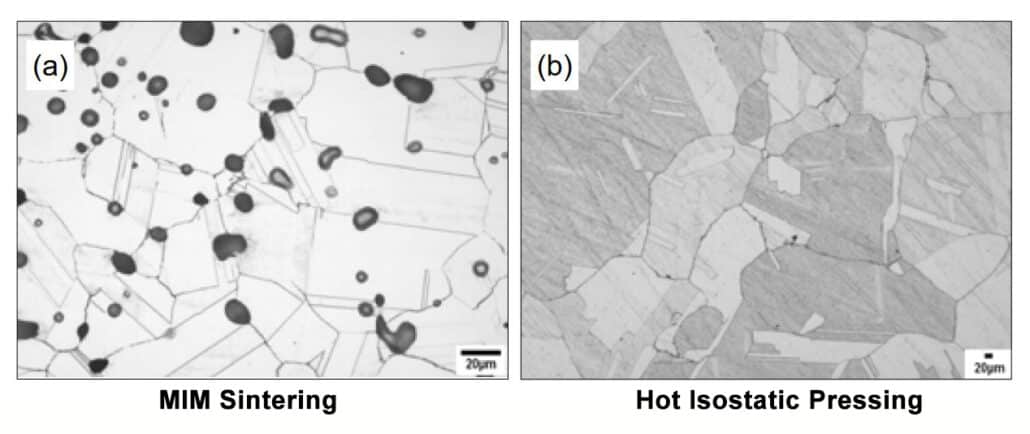
Chemical Composition
Stainless Steel 17-4 | Iron | Nickel | Silicon | Carbon | Chromium | Niobium | Manganese | Copper | Sulfur |
Percent by Weight | BaL. | 3.00-5.00 | 1.00 | 0.07 | 15.50-17.50 | 0.15-0.45 | 1.00 | 3.00-5.00 | 0.03 |
Normally, the mechanical properties of MIM 17-4 PH stainless steel is 10-25% lower than wrought 17-4 PH. The main reasons including:
- Presence defects of sintering: retained pores and grains, residual carbon impurities.
- Elemental loss via evaporation: Cr, Cu, Ni.
- Inclusion of impurities:O, C, N.
Carbon and nitrogen elements stabilize the face-centered cubic austenite phase with slowing sintering. Conversely, body-centered cubic delta ferrite will increase the sintering rate. Furthermore, martensite forms on cooling process from sintering, the precipitation reactions in stainless steel 17-4PH induce high hardness and strength, while retained delta-ferrite reduces strength.
Oxygen is a significant factor in MIM products, stainless steel powders have high initial surface area with oxides coating, these oxygen levels will vary with different powder manufacturing process. These oxides will remove chromium from its corrosion inhibition effect, thus, high oxygen levels in MIM 17-4 PH parts result in low mechanical properties and poor corrosion resistance.
Typical Properties
MIM is an advanced technology to fabricate complex, high-performance stainless steel components. The sintering behavior of stainless steel 17-4 PH depends on powder particle size, peak temperature, heating rate, atmosphere and holding time. There are various factors influence 17-4 PH alloy composition, this finally affects the micro-structure phases, sintering behavior and final properties. The main factors including: Carbon from the powder or binder, oxygen from the powder or atmosphere, nitrogen from the process atmosphere.
Popular applications of 17-4 PH arise from the perfect combination of strength, hardness and corrosion resistance. After heat treatment, the properties’ combination is attractive for aerospace, dental, medical and electronic products. Depending on different composition with variations in Fe, Ni, Cu and Cr. The solidus temperature is around 1405℃, while the liquidus temperature is near 1440℃. In reason of the mechanical properties are sensitive to heat treatment, the hardness reach to 43 HRC, with yield strength from 760 to 1240 MPa, tensile strength from 1000 to 1340 MPa, and fracture elongation between 8 and 14%.
In metal injection molding industry, 17-4 PH stainless steel has popular application due to its excellent combination of strength, hardness and corrosion resistance. Stainless steel 17-4 PH is the most typical precipitation hardened martensitic stainless steel.
- High strength
- High hardness
- Excellent corrosion resistance
- Fracture toughness
- Heat treatment and welding properties
Binder and Debinding Effect
Different binder systems are applied for stainless steel 17-4 PH injection molding, the common binders consist of 60% filler, 30% backbone and 10% surfactant.
Debinding has influence on final properties, as residual binder materials will affect the final oxygen or carbon levels. The first stage of debinding is de-polymerization or solvent extraction, such as paraffin wax dissolves in heptane, polythylene glycol dissolves in hot water. In addition, catalytic debinding also apply fuming nitric acid to extract polyoxymethylene. In the second stage of debinding, the optimal binder removal method is holding at 600 to 1000℃ in hydrogen atmosphere. This stage is also classified as the starting stage of sintering.
Sintering Parameter Effect
In stainless steel 17-4 PH sintering, several parameters interact to determine final density, phase, micro-structure, and properties. With statistical analysis, there are four main factors: particle size, starting oxygen content, sintering atmosphere, heat treatment.
The dominant factor for sintered density is sintering temperature.
Particle Size
During sintering, the initial particle bonding occurs with surface diffusion, smaller particle size with more surface area will increase initial bonding and strengthening. Surface diffusion bonding will replace the particle adhesion by the backbone polymer as binder pyrolysis occurs. As sintering bonding grow between metal particles, grain boundary diffusion requires neck growth to form grain boundaries between particles. Once grain boundary form, the grain size has inverse effect on the sintering rate, it has the main role in sintering when shrinkage starts. However, longer holding time or higher peak temperatures can offset the effect of initial particle size.
Atmosphere
The normal sintering atmosphere option in stainless steel including: hydrogen, nitrogen, hydrogen-nitrogen, argon-hydrogen and vacuum.
Hydrogen or vacuum are the most common sintering atmospheres for stainless steel 17-4 PH. If add carbon, there is significant oxide reduction. Without carbon additive of graphite, both chromium and silicon can retain oxygen. High temperature and higher hydrogen content result in oxide reduction, while a low dew point will ensure this process. After sintering , the cold surface oxidize will form a passive layer of iron, chromium and silicon, which provides corrosion resistance.
Sintering in hydrogen is sensible for carbon and oxygen removal, while vacuum sintering results in evaporation of chromium and copper at high temperature.
In the following table, we can find the comparative properties of stainless steel 17-4 PH in different atmospheres (Hydrogen, Vacuum, Dissociated ammonia).
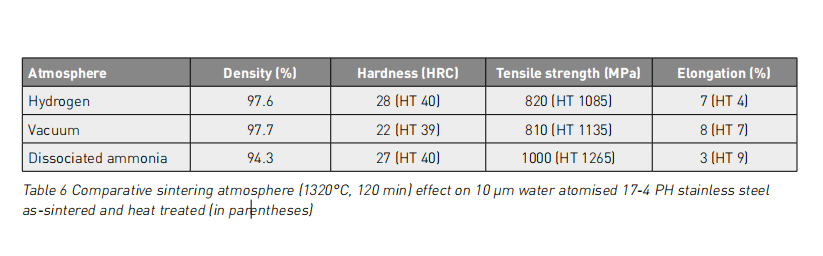
Nitrogen is a potent austenite stabilizer, it affects the martensite formation and final properties of stainless steel. Nitrogen is soluble in austenite, and forms Cr2N precipitates in cooling process. This precipitate will rob the grain boundary area of chromium, and result in rapid corrosion on localized area. Therefore, we need to avoid nitrogen in sintering atmosphere, and cooling parts at rapid rate of 200℃/min below 900℃. In order to suppress chromium nitride formation in stainless steel 17-4 PH.
In addition, graphite vacuum furnaces are successful in vacuum sintering, graphite can create low partial pressure of carbon monoxide in vacuum furnace. It can reduce chromium oxide to chromium at 1300℃ with low CO partial pressure of 0.001
Heating Rate/Temperature
The normal sintering cycles involve binder burnout and impurity removal procedures by heating and holding at different temperatures. Optimal temperature for final polymer removal is near 600℃, while near 1000℃ for impurity reduction.
The sintering shrinkage of stainless steel 17-4PH starts at near 900℃ in dilatometry testing, the peak shrinkage rate is near 1250℃, but full-density (98%) requires peak temperature of 1300℃. However, these high temperatures will evaporate copper and chromium, and result in potential loss of heat treatment and corrosion resistance.
In addition, higher temperatures are instrumental in delta-ferrite formation, this phase will assist the final densification by faster diffusion. From the following micro-structure graph of MIM 17-4PH in sintering, we can notice the white delta-ferrite colonies, and the dark regions of circular oxide pores.
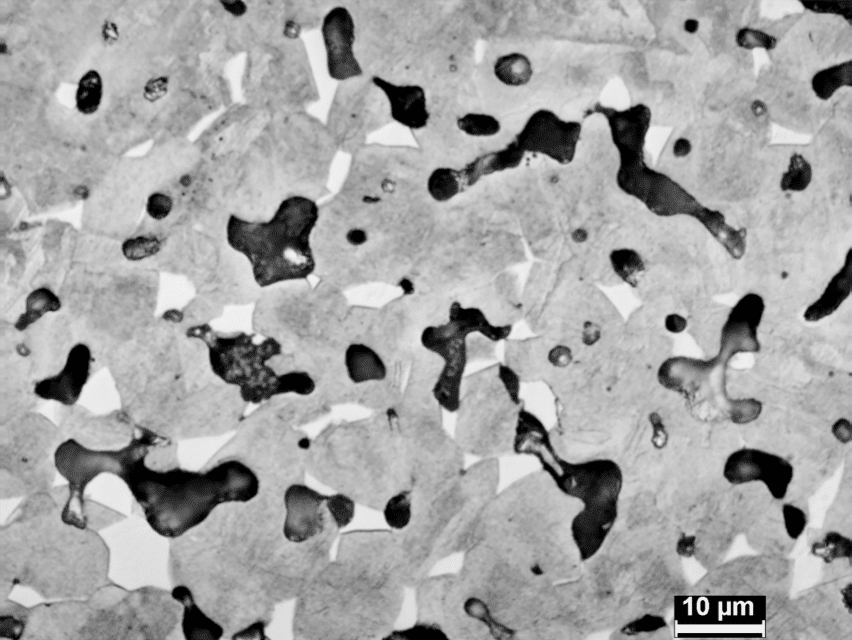
Carbon Control
Carbon is another austenite stabilizer during sintering process. Low retained carbon content levels below 0.1 wt.% in 17-4 will provide higher strength and hardness. The alternation of carbon level will impact phases, densification and mechanical properties of stainless steel 17-4 PH.
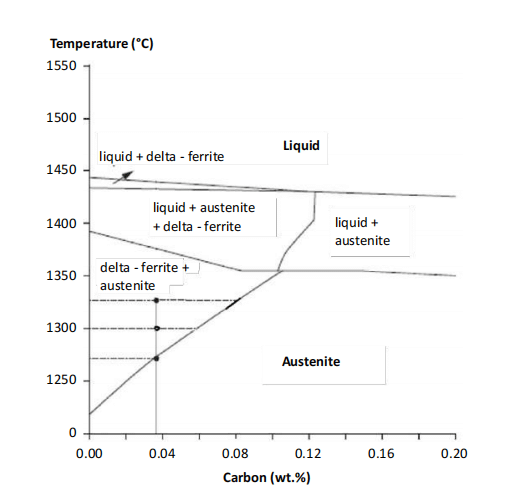
The carbon level depends on various factors in MIM process, including: atomized powder, binder residuals, debinding cycle, sintering atmosphere, initial oxygen, peak sintering temperature. The initial oxygen level is the main factor for final carbon level, as carbon react with oxygen in sintering. Such as, there is 0.03% carbon loss in hydrogen sintering at 1343℃ for 17-4 gas atomized powders. Moreover, carbon contamination also arises from binder residuals, especially at lower sintering temperatures.
The retained carbon levels affect the tensile strength of stainless steel 17-4 in hydrogen and vacuum sintering. No matter in normal sintering of 1300 to 1360℃, or H900, H1100 heat treatment. From the following picture, once carbon concentration reaches to higher levels, there is notable loss of tensile strength.
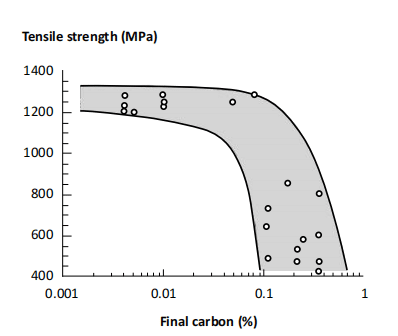
Holding Time
Holding time at the peak temperature in sintering are in the range of 60 to 120 minutes. From the following graph of sintered density versus time and temperature. It indicates a progessive density from 96.3% to 98.3%, as temperature increase from 1240℃ to 1360℃. With 60 minutes holding, the sintering compacts reach full density (98%). In this process, porosity is eliminated, and pore annihilation rate is declined. The main reasons are the exhaustion of porosity and the loss of grain boundaries.
MIM 17–4 Advantages
- High corrosion resistance
- Age-hardening by heat treatment
- Industrial-grade toughness and strength
- Excellent thermal resistance
- Suitable for complex geometry in MIM
Mechanical Properties
As MIM 17-4 PH is applied for structural devices. Strength, hardness and elongation are favorite comparative properties. Furthermore, fatigue, fracture toughness, yield strength are also concerns, which are influenced by several processing factors.
From statistical analysis of different MIM projects, we summarize the average properties of 17-4 PH in the following picture. Nearly 60% of property variation are attributed to sintering parameters.
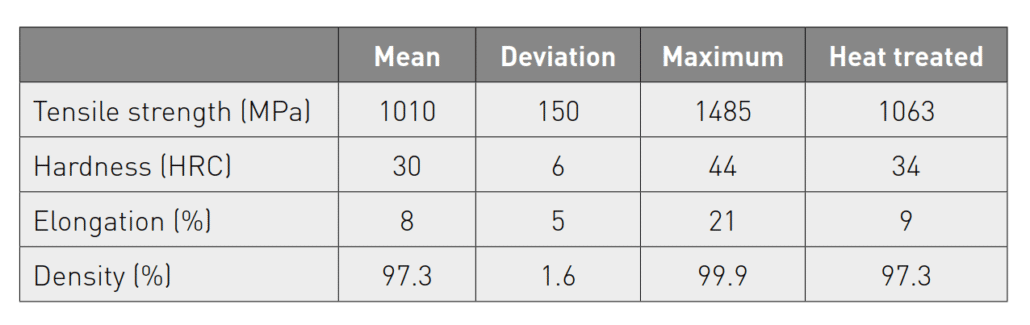
In the MIM industry standard, the minimum properties of stainless steel 17-4 PH are 790 MPa tensile strength, 27 HRC hardness after sintering, 1070 MPa and 33 HRC after heat treating. Both with 4% elongation. After 1350℃ sintering and H900 heat treatment, the tensile strength of stainless steel 17-4PH are 1280 MPa for gas atomized powder and 1136 MPa for water atomized powder. Notice, heat treated tensile strength can reach to 1485 MPa with 9% elongation by gas atomized powder.
Corrosion Resistance
Standard corrosion testing involves various environments, extensive corrosion testing of four sintered stainless steel (304, 316, 430, 17-4) indicate that 17-4 is the least resistant to different environments. Furthermore, wrought material has more corrosion resistance than sintered material, since pores on sintered parts induce local corrosion by concentration polarization. As retained oxygen is a negative factor, there are two common methods to increase corrosion resistance: hydrogen sintering and gas atomized powder.
Bio-compatibility is also relevant to corrosion resistance. Stainless steel 17-4 PH is good in cytotoxicity, but not competitive in overall biocompatibility once compared to titanium and cobalt alloys.
MIM 17-4 PH Application Market
17-4 PH stainless steel provides outstanding mechanical properties at high temperature up to 350℃. It also has good toughness in both vase metal and welds, low temperature heating with short time will minimize warping and scaling.
Aerospace
17-4 stainless steel is an excellent option for aerospace applications with heightened corrosion and thermal resistance. High powder purity and densification can reduce the error change, guarantee the durability of MIM 17-4 products.
Automotive
Stainless steel 17-4 is the most popular materials on automotive manufacturing, as it is easily to machine into various shapes. Metal injection molding technology also expands its capability of complex geometry with significant durability.
Consumer
The excellent corrosion resistance of 17-4 makes it popular for consumer applications with MIM technology. In addition, its high hardness and strength also ensure the seamless work without causing errors.
Conclusion
MIM 17-4 PH achieves tremendous progress on structural property optimization. It provides various attractive combination of sintered properties for many suitable applications. Comparing to powder type, particle size, green density, holding time and other parameters, sintering temperature is the dominant factor for final properties. Moreover, the sintered properties are sensitive to existing phase in sintered materials.
Meanwhile, properties also vary with the phase morphology, sintered density and post-sintering heat treatment. Hot Isostatic Pressing (HIP) improves properties, while sintered density determines properties.
As stainless steel 17-4 PH reach to the forefront of Metal Injection Molding (MIM). ZCMIM relies on MIM technology base, in order to provide more applications for sintered 17-4 PH.