How MIM Work
Introduction
Once you want to manufacture a complex metal part, there are various methods, like die casting, machining, or powder metallurgy. Metal injection molding (MIM) is a different manufacturing way. It mixes metal powder with binder materials, molds these materials into the desired shape, then removes the binder materials and sinter into the final part. MIM technology can produce intricate metal parts with a wide range of metals, including steel, stainless steel, copper, titanium and high-temperature alloys. Metal injection molding has widespread commercial application in last twenty years, include automotive, medical, electronic, tooling and consuming.
You might be familiar with powdered metal or powder metallurgy (PM), parts as bearing, bushing and micro gears. PM technology forms metal power with compression in die molds, and then sinters into net shape. These related process also use metal particles. However, MIM metal powders are much finer than PM, MIM is a complete different metal manufacturing process with PM.
MIM technology can fabricate complex parts economically with structural metals, it can provide significant cost saving for manufacturers. This technology will reduce parts cost in many cases, especially for high volume production. In addition, it also can replace assembly operation of two or more parts with just one single MIM part, and eliminate the assembly cost of those parts.
Power to Part
MIM metal powders are very fine, with particles size of 20 micron or less. These fine powders are made by different production process, including molten metal atomized with high velocity stream of water or gas.
MIM Forming Process
Metal injection molding process starts with compounding the feedstock, which is a combination of metal powders and binder materials. The binder materials are a mixture of plastic and wax materials. It will melt and hold metal particles in suspension once these feedstocks flow into mold cavities. Most feedstock is 60% metal powder and 40% binder materials in volume.
Feeedstock will be heated and forced into mold cavities, then removed from molds. These molded parts have the same shapes as final parts, but have much larger dimensions. We call parts in this process–green parts.
Debinding is the next step, it will remove most binder materials. We have different debinding ways for different binder system, such as thermal, catalytic and solvent debinding. After this stage, there are a small mounts of binder materials to hold parts shape, and nearly 40% of porous on parts surface. These parts are called–brown parts.
MIM Sintering Process
Finally, we will set brown parts on ceramic trays with fixtures support. Then place brown parts into furnaces to remove leftover binder materials and sinter into net metal shape parts. Sintering is normally in a vacuum, hydrogen or other gaseous atmosphere. This depends on metal alloy chemical requirement. Such as, metal with oxide form on the particle surface is in a hydrogen atmosphere to remove oxide layers.
In sintering furnaces, the temperature rise to remove the remaining binder materials. Then reach to approximate 90% of metal melting temperature. At this point, metal powers will bond and join together. After sintering, most MIM parts will achieve 95-98% of full density with 2-5% equal dispersed voids. MIM parts with distort in sintering can be coined or straightened in post operation. Heat isostatic pressing (HIP) can increase final MIM parts density to 100% as requirement. In addition, machining, heat treating, plating and other processes can be applied to sintered parts.
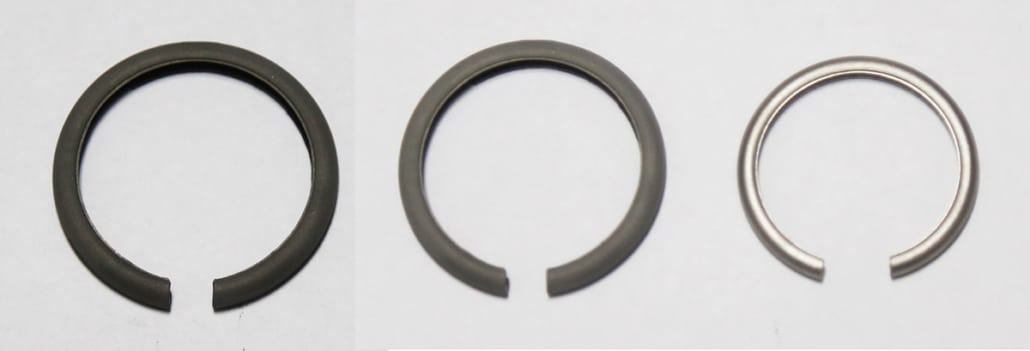
Economic MIM Production
As MIM parts are produced in precision injection molds, which is similar as plastic injection molds. But MIM molds will be more expensive, normally a MIM mold will cost 30% percent than an equivalent plastic mold. In reason of binder compounds properties, MIM molds should fit together more tightly than plastic molds, and this give rise to tighter dimension tolerances for MIM parts. The cost of MIM injection molds varies tremendously by many factors, most multiple-cavity molds cost will be thousands of dollars.
In order to make MIM economical, we need to amortize the tooling cost over all parts production, so our MIM technology will be cost-effective only for high volume production of more than 10,000 pieces. Our typical quantities can reach to hundreds of thousands, or even millions.
MIM process provide excellent performance for small-size parts, our recommended weight is 50 gram or less, while for special requirement, our typical maximum weight can achieve to 100 to 200 gram. Our tolerances on finished parts are normally ± 0.03% or even closer. While for long and big parts, features-to-features tolerance will be challenging in control.
MIM is a professional manufacturing process for small, complicate, high volume parts. Some precise parts cannot be produced economically without MIM.
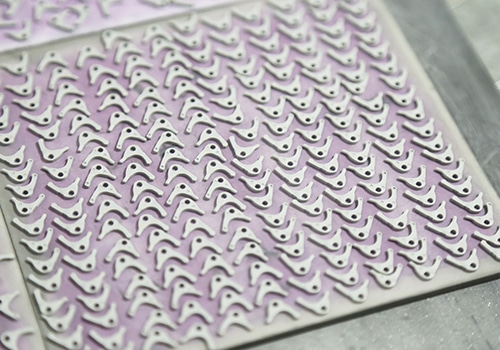
Metal Property Mystery
MIM parts perform excellent mechanical properties close to wrought metals on ultimate tensile strength. However, comparing to forged or wrought metal parts of the same alloy, the remaining porosity in complete MIM parts will impact dynamic properties such as impact and fatigue strength.
The overall uniformity and fine micro-structure of MIM metal can improve its consistent properties. For wrought metals, the mechanical properties in the rolling direction are different from the transverse direction. While MIM parts are quite uniform in all directions. MIM also has performance advantages over casting, which may create large, irregular pores and non-uniform chemical composition in the melting and solidification process.
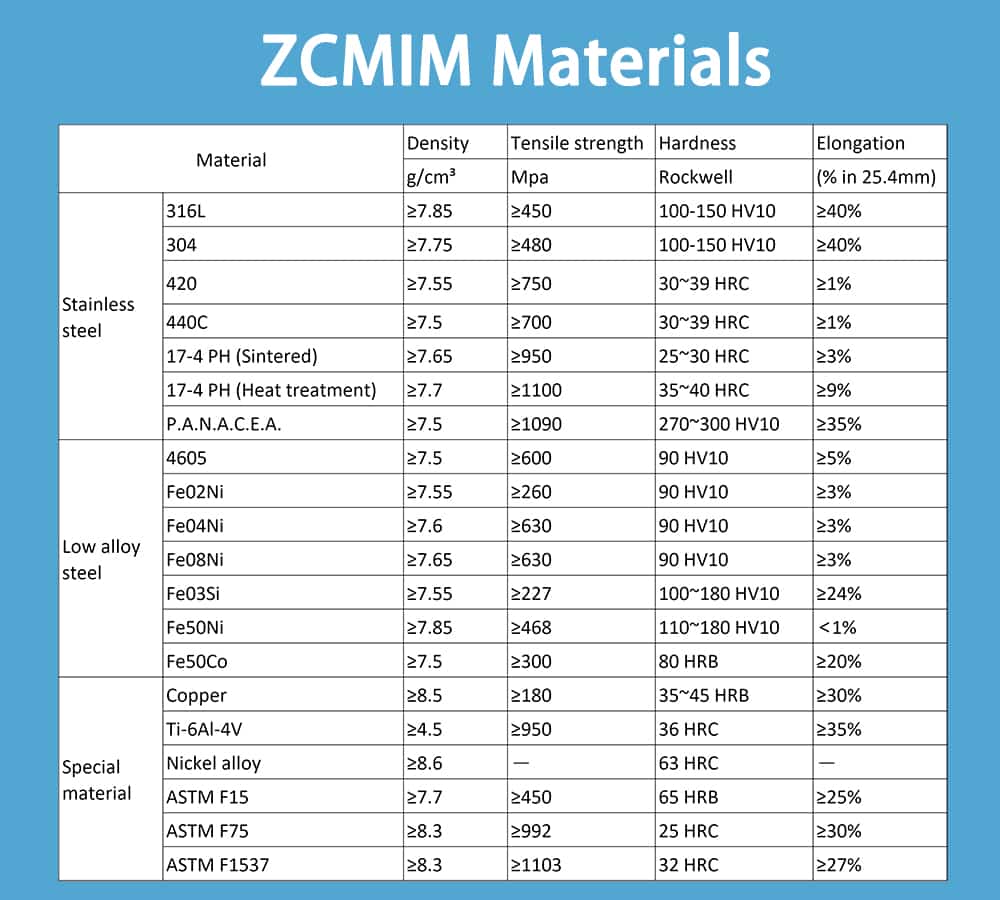
Learning to MIM
In MIM design, most design guidelines for MIM parts are the same as plastic injection-molded parts, such as the same recommendations of uniform wall thickness and ribs for strengthening. However, we also need to consider MIM parts behaviors in sintering process, and design special features to prevent sagging or other deformation. We can apply special fixtures to support parts structure during sintering, or straighten parts afterward. But the ideal design is to make the MIM part support itself without deformation in sintering furnaces.
MIM material selection is a challenges process. Once you start cooperation with us, you just need to specify your part’s mechanical properties, then our engineering team will assist you to select the perfect material for your project. In addition, we also provide custom MIM materials for your higher performance requirement.
Metal injection molding is a powerful metal manufacturing technology, it is not ideal for any part production in every application. However, for high volume production, MIM can solve design issues and save assembly cost, which is impossible with other manufacturing technologies.
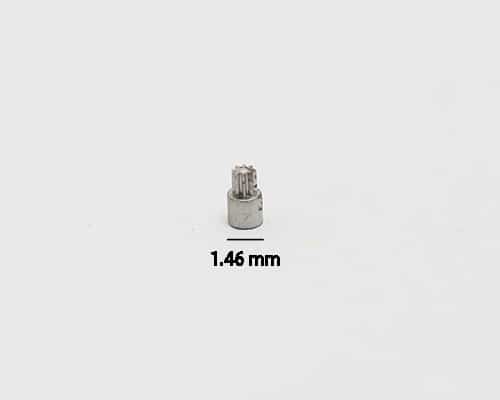
Our experienced MIM engineers will help you tune a new design and select the right material. If you are looking for a cost-effective metal manufacturing way, or creating a single molded part without assembly. Contact our engineering team for professional recommendations.