MIM Polishing
Introduction
MIM Polishing can be used widely for aesthetic improvement. In order to satisfy both mechanical and cosmetic requirement. In metal injection molding (MIM) projects, we always manufacture intricate parts for functional usage. While sometimes, we also need the additional process of polishing to increase parts appearance, in order to achieve customer’s excellent surface finish requirement.
As sintered parts in MIM have corresponding mechanical and physical properties, Polishing procedure can be used widely for aesthetic improvement without any application affection. In ZCMIM, we had produced millions of MIM parts with polishing process, all these MIM parts can satisfy both mechanical and cosmetic requirement. There is an obvious case in ZCMIM, which can assist you comprehend the excellent improvement of MIM polishing.
Polishing Preparation
MIM Parts Selection
Watch frame is the most common product in MIM, in reason of MIM has high productivity, it can manufacture millions of watch frame in short time with high tolerance.
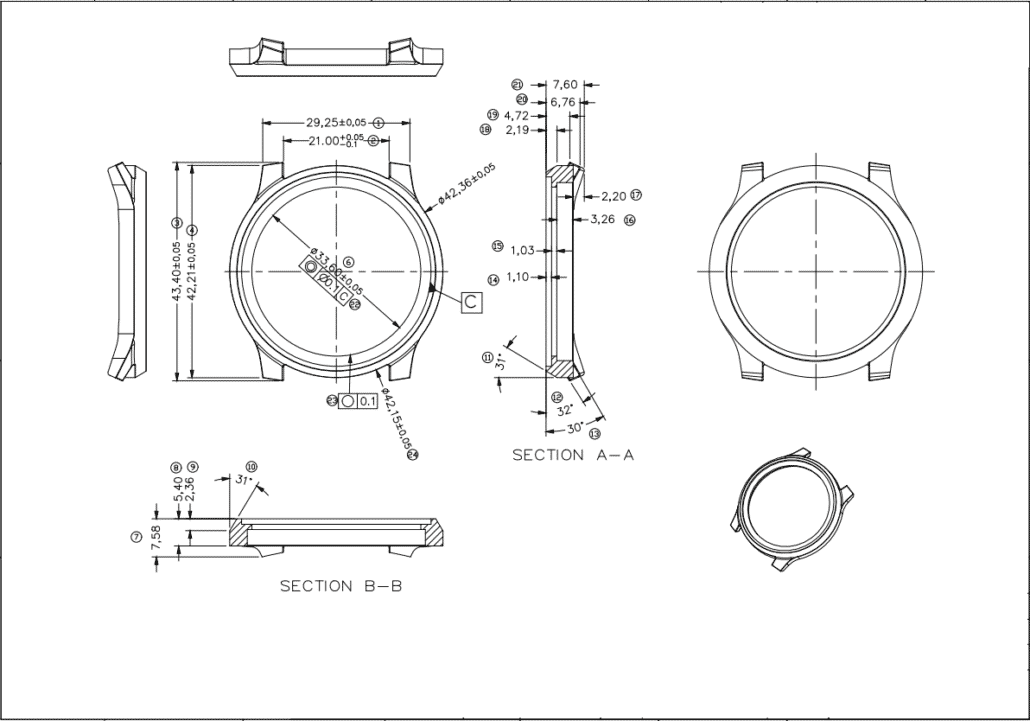
From 2D design drawing, we can realize this design is a common watch frame without extreme complex structure. However, the main point of part appearance is to achieve high smooth surface. In order to satisfy aesthetic requirement in normal applications.
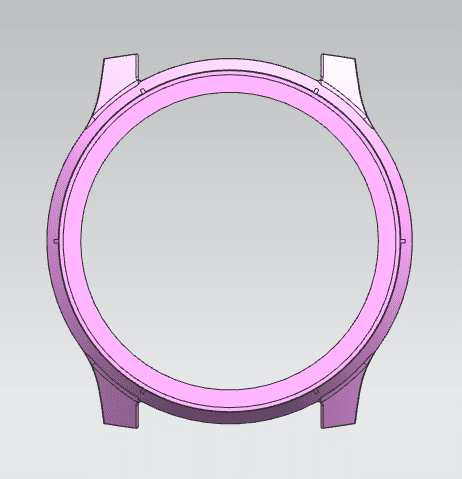
MIM polishing as an additional process will increase the total cost of parts production, normally we recommend applying this process for application with surface appearance requirement. For normal functional application inside or invisible, we don’t require MIM polishing.
MIM Material Selection
MIM polishing can be used for any MIM parts with various materials. However, in order to achieve the best surface appearance, we recommend the BASF Catamold 316L. As in our thousands MIM projects, tthesehis materials with MIM polishing process will provide the best mirror polishing appearance. We can check the following photo with BASF Catamold 316L watch frame after polishing.
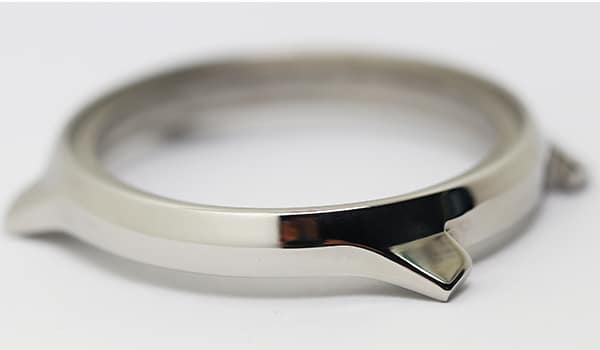
MIM Polishing Machines
In ZCMIM, we normally apply 3 common polishing machines:
Single-disc Polishing Machine
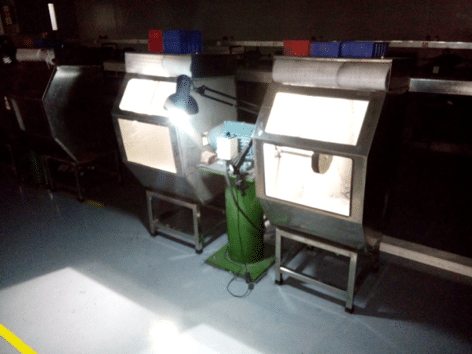
Single disc polishing machine is the most common polishing machine, we apply this machine in almost every MIM polishing project. This machine applies high-speed rotation of roller and grinding agent to treat work-pieces surface, the friction cutting between grinding wheel and work-pieces will eliminate needless materials on part surface to achieve required appearance. Generally, the first step of polishing is rough polishing with a hemp roller.
In order to satisfy different surface polishing requirement, we provide different rollers and wax, the following graph listing our common roller and wax applications.
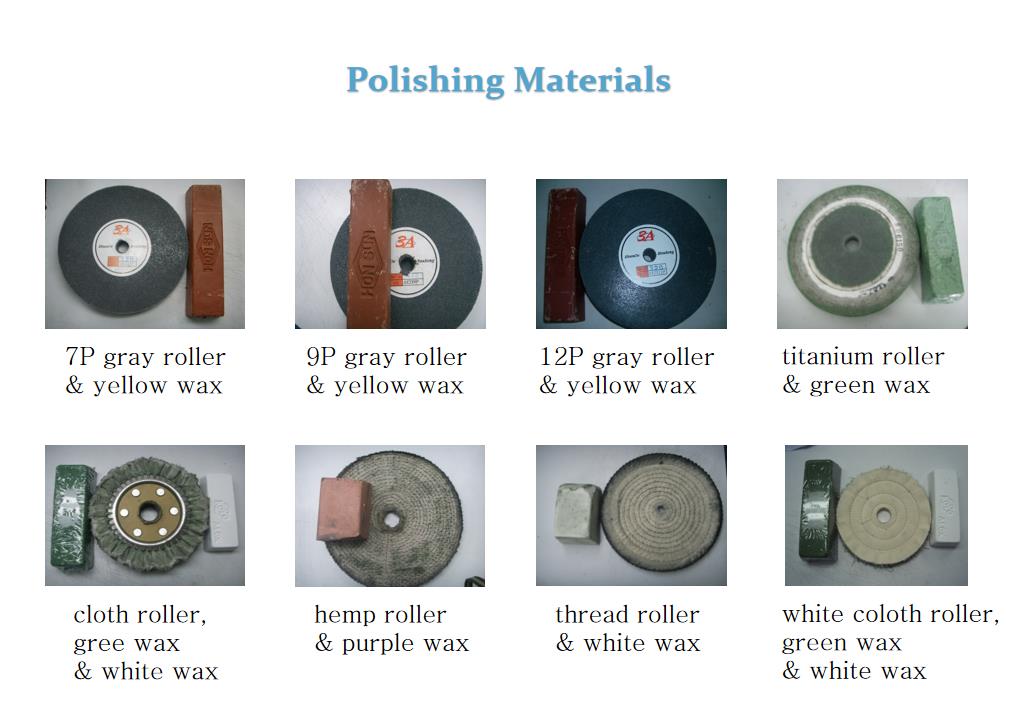
Double-disc Polishing Machine
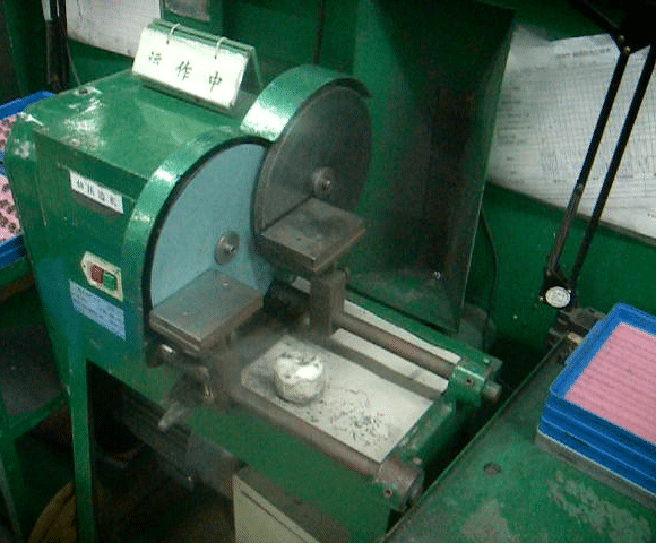
Double disc polishing machine apply high-speed rotating sandpaper with grinding agent to friction mill work-pieces surface. In order to eliminate parts surface materials to achieve required roughness. However, this machine only can polish MIM parts with flat or regular curved surface. The general sandpaper types are 400#, 600#, 800#, 1500#, 2000#, 3000#, the larger size of sandpaper will polish finer surface finish. The common grinding agent are oil wax and yellow wax.
Water Sand Polishing Machine
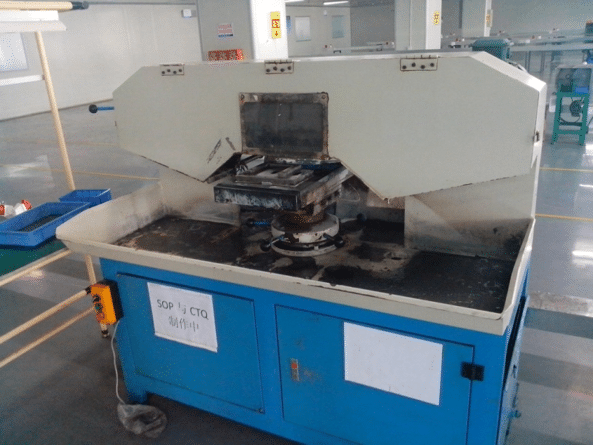
Water sand polishing machine apply high-speed rotation sand belt to friction mill MIM parts surface, cut irregular materials on MIM parts surface to reach the required roughness. This machine is able to process MIM parts with plane surface. The normal sand belt type are A16(1200#) and A6(3000#), the larger size of sand belt can produce more fine surface after treatment. This machine also need water-soluble cutting fluid as grinding agent.
MIM Polishing Process
At ZCMIM, most of our MIM parts have complex structure. This determines that the single disc polishing machine is suitable for our normal MIM polishing process.
Polishing Materials Application
Normally, we will apply hemp roller and titanium roller for rough polishing as first step. Then thread roller for the last fine polishing step.
Yellow wax is applied with gray roller for rough polishing, especially for stainless steel, steel and titanium. But not suitable for final fine polishing step.
Green wax is applied with titanium roller for rough polishing, with thread roller for fine polishing.
White wax is applied with cloth roller for fine polishing, which also modify lighting effect of roller pattern. But not suitable for rough polishing step.
Polishing Procedure
- Before polishing, we should select different grinding roller and wax according to different MIM part surface requirement.
- In polishing process, the force in polishing should be uniform, in order to avoid deformation.
- For hole or mark position, polishing process should be more carefully to avoid any deformation.
- Waxing the grinding wheel regularly during polishing process, in order to avoid too high temperature on parts surface with abnormal color.
- We should clean and replace grinding fixture regularly, in order to avoid wax accumulation and fixture abrasion. This will result to grinding deformation or excessive fillet.
- After polishing, handle all parts with care and place in order, avoid stack together. We should check parts surface, identify error like scraping, seal, sand hole etc.
Polishing Advantage & Limitation
Sintered MIM parts have rough surface finish, in reason of its natural manufacturing methods. Very fine metal powder particles bond with each other at sintering furnace with high temperature. Therefore, it results in irregular metal particles’ accumulation on sintered parts surface. Finally, the surface displays roughness without brightness as following picture.
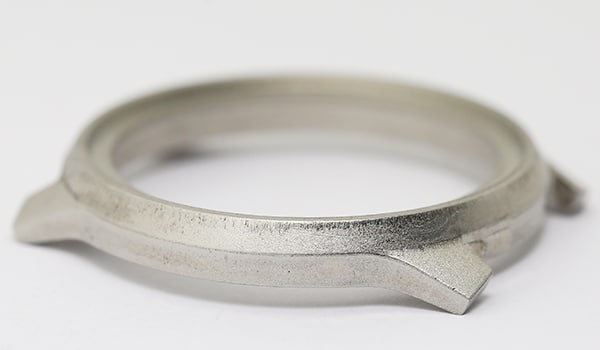
MIM Polishing Advantages
- It provides final parts excellent leveling property and high brightness.
- The MIM polishing will also increase metal material durability, chemical corrosion resistance.
- It enhances metal material’s color and reflectivity.
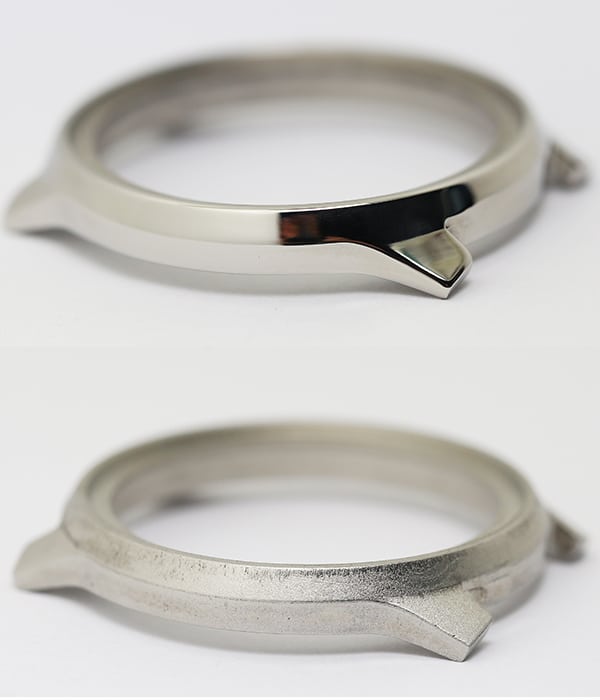
MIM Polishing Limitation
- MIM Polishing is a high labor intensity process.
- Intricate MIM parts structure will affect final polishing appearance.
- MIM polishing is cost-effective for simple MIM parts with small size.
Conclusion
MIM polishing provides an excellent way to improve MIM parts surface finish without any mechanical and chemical properties influence. ZCMIM had supplied millions of parts for our customers with high reputation. Please contact us for your next new MIM project.